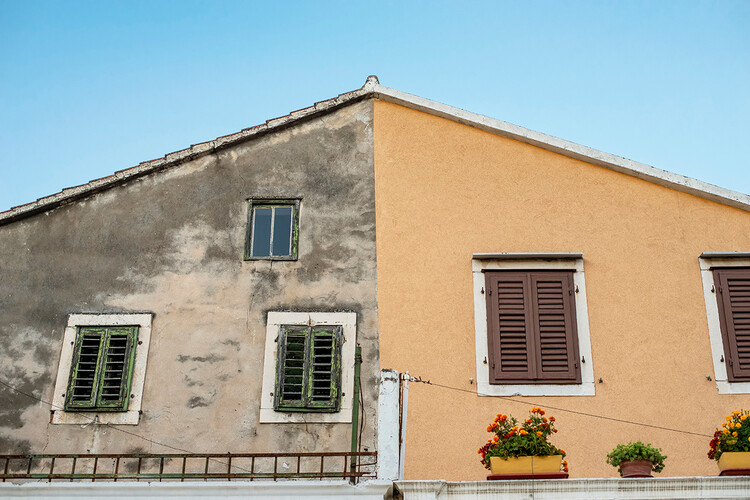
Construction practices across the world, as well as the types and uses of building materials, have been identified as key factors that impact global warming. Studies have shown that the building sector will play a central role in achieving the UN Climate Change Conference (COP26) CO2 emissions reduction targets for 2030 and net zero CO2 emissions by 2050.
The construction sector's support for the achievement of these targets must focus on sustainable construction, which entails environmentally-friendly structures that consume less energy and have smaller or even net zero carbon footprints.
Green buildings are structures that, in their design, construction or operation, reduce or eliminate negative impacts on our climate and natural environment. They preserve precious natural resources and improve quality of life.
What makes buildings green and how are they better?
Two of the most important characteristics which make a building ‘green’, as per the World Green Building Council, are:
Efficient Buildings:
- Efficient use of energy and other resources
- A design that enables adaptation to a changing environment
Better Living Conditions:
- Use of materials that are non-toxic, ethical, and sustainable
- Good indoor environmental air quality
A green building, therefore, in its design, construction and operation, not only contributes to a cleaner and greener environment with high energy efficiency and reduced wastage, but also provides a better quality of life for occupants.
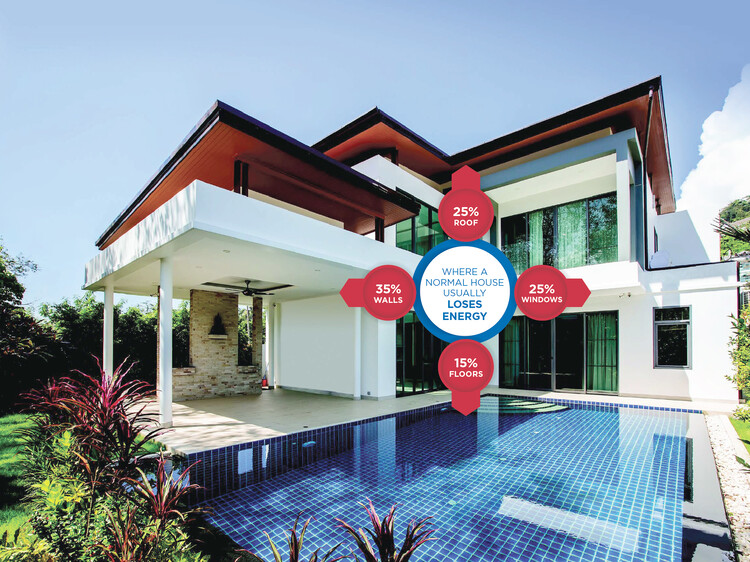
How does Terraco help customers build green buildings?
Terraco is a leader in the design, formulation and production of environmentally friendly finishing materials and energy efficient systems for the construction industry since 1980, offering solutions that help ensure buildings are both energy efficient and sustainable.
On average, people spend the majority of their time inside a building or a structure. It is therefore extremely important that these buildings provide living spaces conducive to good occupant health and wellbeing.
When discussing green buildings, some of the key challenges that need to be considered are:
Energy Efficiency in Older Buildings
Older uninsulated buildings were not designed to regulate interior air temperature efficiently. As per studies conducted by the Renovate Europe forum, due to the high cost of energy, up to 10.8% of the overall population in Europe is unable to properly heat or air condition their homes in cold winters or hot summers. European countries with the oldest building stock consistently record the highest mortality rates in extreme cold winters and hot summers due to “energy poverty”.
Impact of Volatile Organic Compounds (VOC) on air quality
VOCs in building materials negatively impact indoor air quality and can cause long term health issues for occupants after an extended period of exposure.
Damp Buildings
Over 80 million people in European countries live in old uninsulated buildings which are extremely expensive to heat. The occupants of these buildings often do not heat their homes adequately, leading to damp conditions with condensation in many rooms, which in turn leads to mould and fungal growth on walls. The occupants of these buildings are at a much higher risk of respiratory ailments.
CHALLENGE 1: Energy Efficiency in Old Buildings
The COVID-19 crisis has brought older uninsulated buildings into sharper focus. Throughout the pandemic, in view of work from home initiatives, homes have become an even greater focal point of daily life for millions across the world. And even post-pandemic, roughly 48% of employees continue to work from home.
These older uninsulated building are now being occupied and heated or cooled all day, with the consequent higher energy demand and exponential increase in cost to heat or cool these inefficient buildings. This trend has been further impacted by current macro-economic and geopolitical turmoil which has led to spiraling energy costs. This ultimately drives a requirement to improve older buildings' energy efficiency on an unprecedented scale.
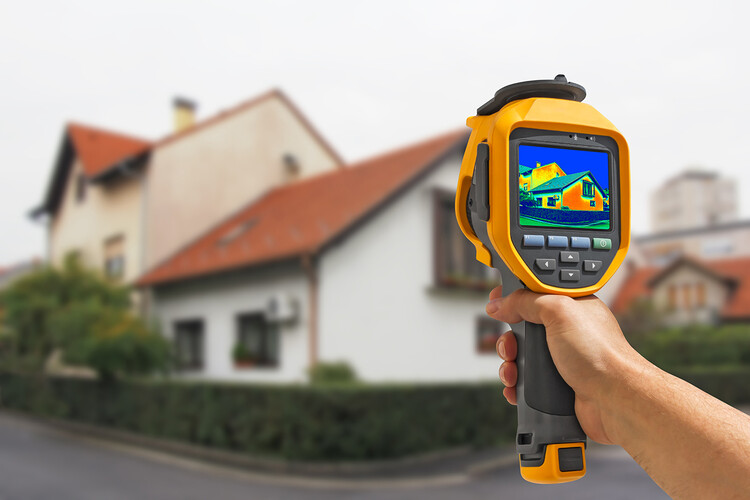
The European Union is trying to tackle energy poverty in buildings and the high energy costs crisis through its Renovation Wave initiatives which offers a unique opportunity to rethink, redesign and modernise older building stock to make them fit for a greener, sustainable society.
Policymakers and authorities play a key role in driving initiatives that are focused towards making buildings more energy-efficient, less carbon-intensive and more sustainable. In the Middle East, government initiatives such as the UAE 2040 masterplan and Saudi Arabia’s 2030 vision are catalysts for more innovations in the construction industry which will facilitate bolder and more aggressive approaches to sustainable renovations.
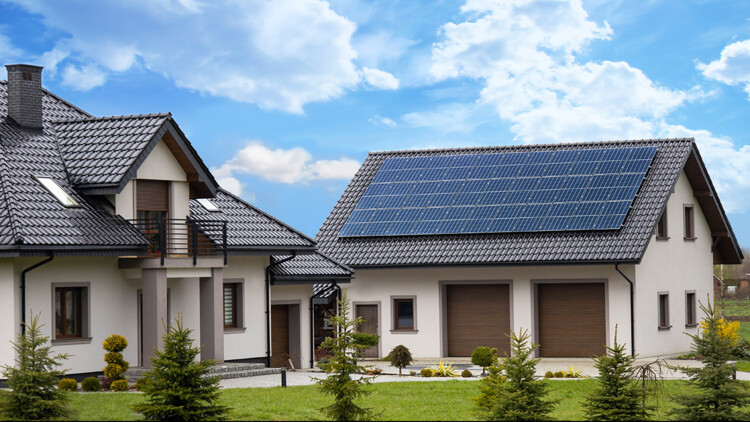
Today, roughly 11% of the existing building stock in the EU undergoes some level of renovation each year. It is critical that energy efficiency is at the forefront when these works are planned and funded.
Exterior Insulation Finishing Systems (EIFS), such as Terraco EIFS, can help overcome the challenge of energy poverty and provide a pleasant, ambient living condition for occupants.
Exterior Insulation Finishing Systems are considered a key solution that are available to achieve the efficient use of energy and other resources within a new or existing building. In fact, many older buildings are rejuvenated and given a major facelift using EIFS, which is installed directly over the existing old exterior facades. Internal living space is not sacrificed and there is no need for occupants to vacate the building while installing, which makes EIFS perfect for renovation work.
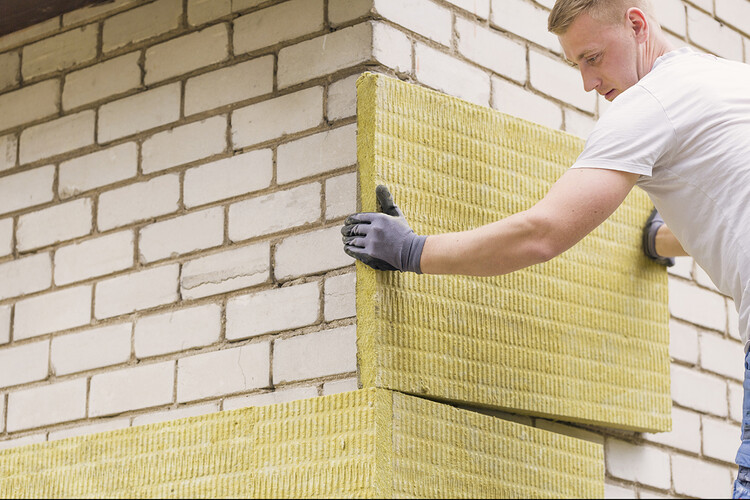
However, it is important to note that EIFS is a complex system that consists of different products and components such as insulation materials, bonding agents, accessories, adhesives and mortars, finishing products that are designed to work together. The efficacy of the complete EIFS system depends on the sum of all parts involved. Therefore, it is imperative that such EIFS systems are certified by the relevant authorities and should be applied only by trained EIFS applicators and installers.
Terraco has been pioneering the development and production of Exterior Insulation Finishing Systems since the 1980's and has achieved numerous international EIFS quality certifications and approvals. Some of these include EOTA (European Organisation for Technical Assessment), BBA (British Board of Agrément) as well as certifications from several other government bodies in Ireland, Turkey, China, South Korea, UAE and many more. In addition, Terraco is a member of the EAE European Association for External Thermal Insulation Composite Systems (ETICS), the common European nomenclature for EIFS.
The versatility and durability of Terraco EIFS makes it ideal for new builds as well as renovation projects, as it offers design flexibility that enables adaptation to a changing environment. Terraco EIFS has been successfully used in projects across the world, many of which have had complex design requirements. Depending on the project, the result is potential energy savings of up to 50% for buildings that are applied with Terraco EIFS.
It also helps reduce the risk for thermal bridging and condensation on internal walls, mitigating the risk of condensation and dampness by allowing surfaces to stay dry and thus avoiding mould or fungal propagation thereby improving indoor air quality.
CHALLENGE 2: Impact of Volatile Organic Compounds (VOC) on air quality
A focused approach from the construction industry and regulators is required to meet this challenge, for which Zero VOC or Ultra Low VOC products should be used during the construction process. VOCs are emitted as gases from some construction products and may have adverse health effects after long-term exposure. Concentrations of many VOCs are consistently higher indoors (up to ten times higher) than outdoors.
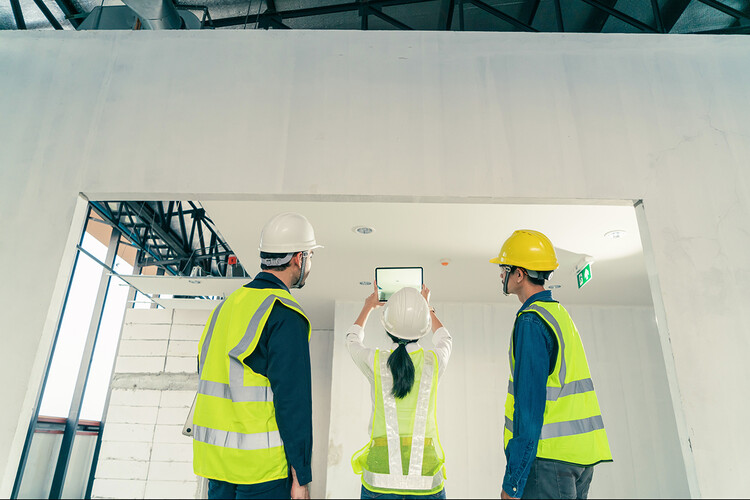
This is a key factor as to why Terraco has never produced any solvent based or high emission product and remains committed to producing products that are non-toxic, environmentally friendly and sustainable.
Most importantly, Terraco’s EcoLife range is completely free of Volatile Organic Compounds (VOCs), formaldehyde and other potentially harmful emissions. These products are special formulated to ensure they are ecologically friendly and natural and the EcoLife range of products comply with the most stringent international VOC standards and regulations.
CHALLENGE 3: Damp Buildings
Excessive moisture in a building can be a major concern for occupants and condensation on uninsulated walls is a major cause of mould or fungi growth. This is exacerbated in humid, poorly ventilated, occasionally heated buildings, leading to growth in the corners of bathrooms, kitchens, junctions of walls and doors, windows and surrounding AC vents. Mould and mildew growth may also develop in unseen areas of the house such as behind wallpaper and within AC ducts.
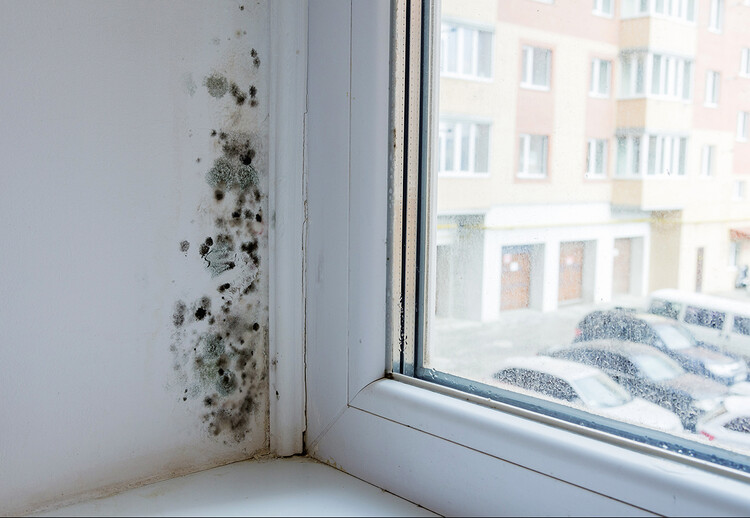
Mould may produce toxins that can cause long-lasting harm to the people residing in the house and prolonged exposure can potentially cause pulmonary fibrosis or lung scarring. In severe cases, these can be cancerous as well.
The use of the Terraco EIFS Systems to insulate external walls in buildings eliminates the condensation risk arising from a poorly insulated facade. These solutions can help customers transform their building to a healthy environment and achieve Green Building status.
For over 40 years, Terraco has been developing products and solutions that help reduce the carbon footprint of buildings and support customers to comply with environmental regulations and to achieve their sustainability goals. Terraco’s products positively contribute to addressing the three challenges set out above: improving energy efficiency in old buildings, improving the internal environment and reducing the risk for damp and mould due to thermal bridging. Terraco continues to engage with and develop innovative new green building technologies with a clear vision to provide sustainable quality solutions for the construction industry.