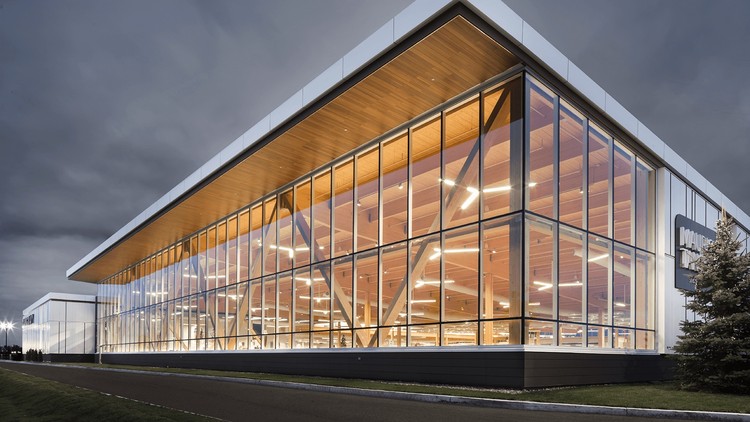
When it comes to commercial and industrial buildings that need to stand the test of time, wood is proving it has the necessary resilience and strength, while offering unique advantages over steel and concrete. In retail and office spaces, wood not only offers remarkable durability, but introduces a much-desired aesthetic warmth once absent from such environments. Adding mass timber to these spaces is a kind of modern-day revival of the century-old timber post-and-beam buildings of the past. What’s old becomes new again, but with all the state-of-the-art technologies and sustainable features expected in today’s commercial buildings.
1. Cost-effectiveness
Construction data (1) shows that mid-rise buildings across the United States cost an average of 23% more to build out of concrete than wood framing and steel-framed buildings are 41% more expensive when compared to wood. For example, in 2017, the average price for steel mid-rise buildings was $208.4/square foot and for concrete came in at $156.5/square foot, compared to wood at $119.7/square foot. In North America, these cost savings come from differences in material and construction costs, yet wood-framed buildings still meet all code requirements for safety and performance. Many communities also have a large pool of contractors skilled and experienced with wood construction, keeping labor costs competitive and construction time-efficient (2).
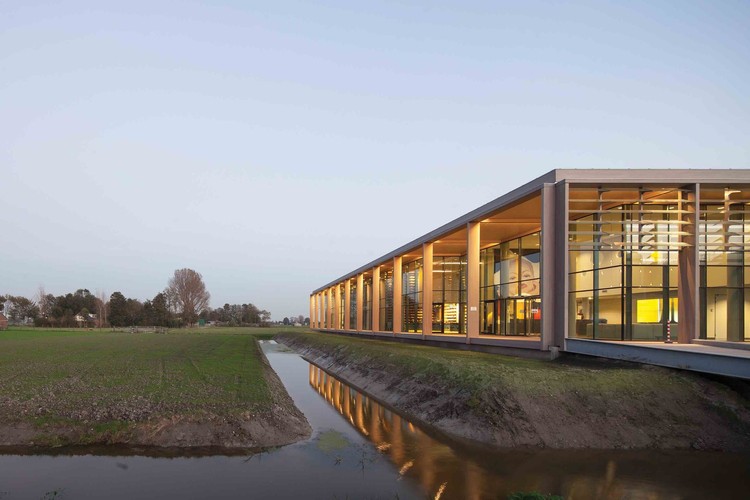
2. Versatility and adaptability
A feature of commercial and industrial buildings is that they often need to be flexible as tenants’ needs change over time. For this reason, spaces are often designed to be as open and unobstructed as possible. When it comes to roof framing, there are multiple wood options available to achieve the long spans necessary for an open floor plan. Truss roofs are strong, economical, and quick to install. They can be engineered and manufactured in complex shapes and configurations thanks to sophisticated software and allow easy coordination with mechanical, electrical, and plumbing systems. Wooden I-joist roofs work similarly to their steel counterparts, with the top and bottom flanges resisting bending and the center web resisting shear forces. I-joists are typically used for flat or low-sloped roofs with spans up to approximately 30 feet. For buildings with larger structural grids, a panelized wood roof system can be cost-effective due to its lower material costs, quick installation time, and insulation. In North America, both all-wood and hybrid panelized systems are common.
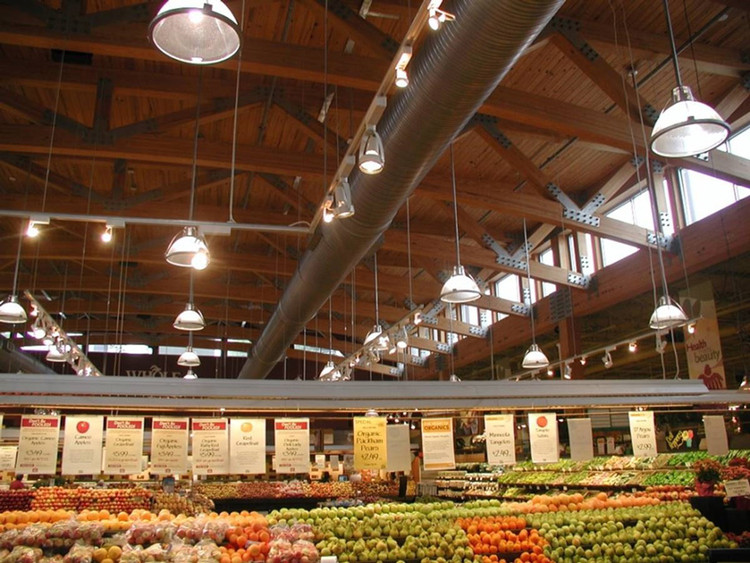
3. Ease of use
More and more building components are now able to be built off-site and simply assembled when they arrive. Especially with heavy timber buildings, the offsite prefabrication of various elements means a reduction in onsite construction time, making structural wood buildings relatively fast and efficient to construct. Timber buildings can also be constructed year-round in most climates and any onsite adjustments are simple and quick to accomplish particularly given the flexibility and versatility of light-frame wood construction. Using wood can also be an advantage for tight, urban job sites, where finding the space for concrete delivery and mixing or steel fabrication can be challenging. Wood can often be sourced locally and therefore delivered quickly and experienced wood contractors are often widely available.
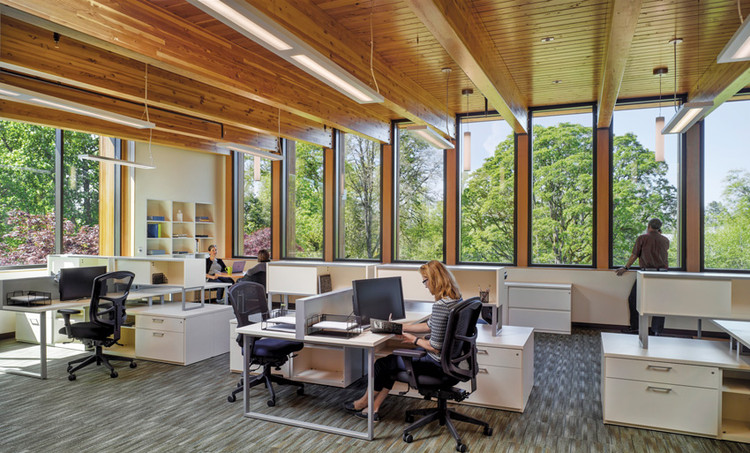
4. Sustainability
Wood is often a popular choice for projects focused on sustainability and the use of renewable building materials. To evaluate the opportunities for wood construction in big box stores, specifically, WoodWorks commissioned a life-cycle assessment (LCA) study comparing a one-story, 54,800 square foot steel-framed big box store in California to a comparable building constructed of wood materials. The two buildings have the same geometry, structural layout, gross floor area, and floor plan, but the LCA concluded that the wood building’s environmental impacts are lower than the steel building’s for all indicators except ozone depletion (for which wood was 5% higher). The impacts were analyzed from raw materials through demolition/disposal and also the additional step of recovery/recycling/reuse. Compared to the steel building, the wood building saves 642 metric tonnes of carbon dioxide equivalent and 9,116 gigajoules of nonrenewable energy use. For the raw material supply and manufacturing phase, the wood building averages 30% less impact across all indicators and for end-of-life transport the wood building has 11% less impact across all indicators.
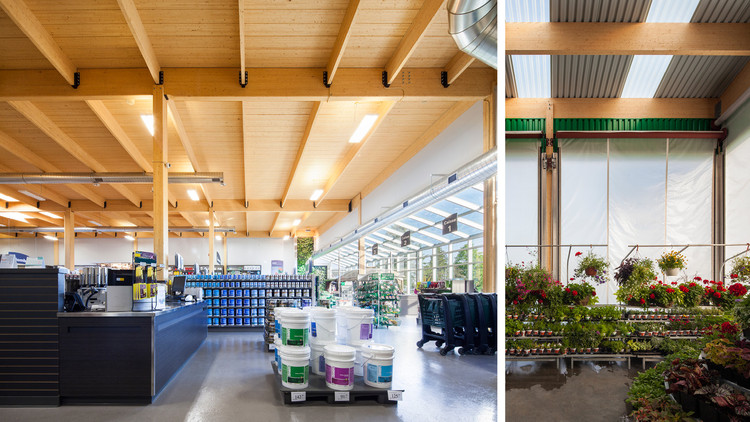
5. Aesthetics and biophilic benefits
Wood's natural beauty can add warmth, texture, and character to any space and studies have shown that people have positive associations with wood and find it visually appealing. Exposed wood trusses or heavy timber columns add immediate interest to a commercial building and set it apart from the vast field of otherwise similar spaces. Designers are also increasing drawn to the biophilic benefits provided by wood. Biophilia posits that humans possess an innate tendency to seek connections with nature. Through the use of daylight and natural materials, including wood, designs that bring nature into a space are thought to be calming and even increase productivity.
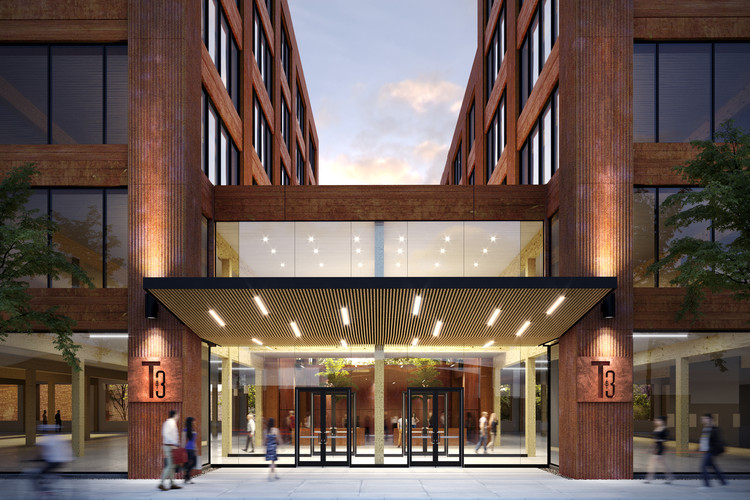
6. Choice and customization
“Wood construction” doesn’t refer to just one type of system or product. Options include traditional dimension lumber framing, but expand to also encompass exposed mass timber and products like cross-laminated timber (CLT), nail-laminated timber (NLT), and glued-laminated timber (glulam). Among these options, the objectives of nearly any low-rise commercial project can be met. Roof framing options were discussed above, but wall-framing can be nearly as varied. Dimension lumber can be either solid-sawn or finger-jointed (shorter sections of wood glued together into longer members), or else glulam framing or structural composite lumber (SCL) products may be used as well. Even “tall walls” 20 feet and higher are possible with wood construction via larger lumber sizes or engineered wood products. Each system has different advantages and the choice of system is driven by the project’s demands, but wood construction is customizable and flexible enough to meet those needs.
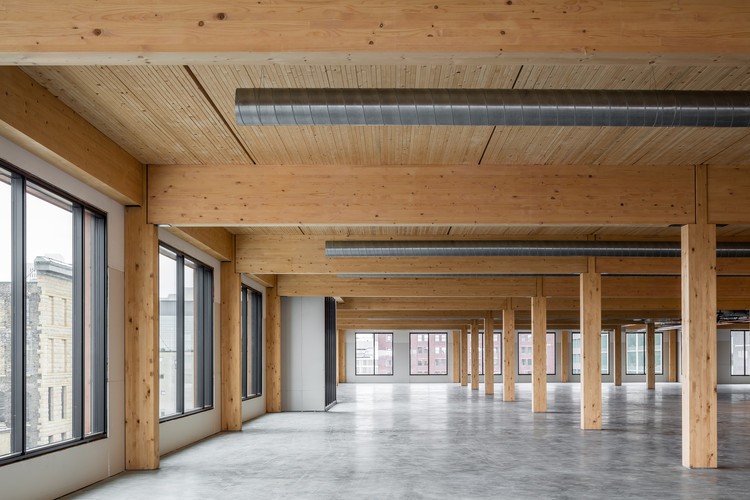
7. Durability
When wood is properly maintained, it can last hundreds of years. Historic examples across the world have stood for centuries and with today’s modern wood preservatives, this natural durability can be enhanced. When treated and maintained correctly, wood can withstand the elements and is well-suited to almost any climate. Heavy timber construction can even inherently resist fire by developing an outer layer of char while remaining structurally stable. Heavy timber, as well as some of the next-generation lumber products mentioned throughout this article, are also enabling increased dimensional stability and strength and greater long-span capabilities to withstand the test of time. Wood buildings, via their aesthetics and comfort, also tend to be valuable to and appreciated by their occupants, potentially decreasing the risk of demolition due to something as ephemeral as changing tastes.
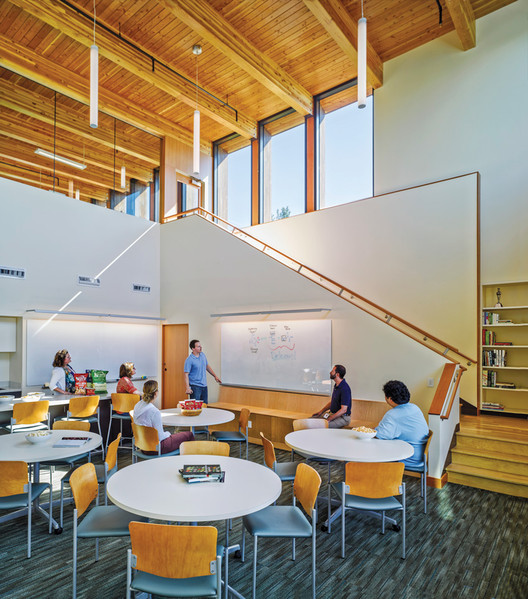
To learn more visit www.thinkwood.com.
[1] FP Innovations/Dodge Construction, U.S. average based on permit values for 3-5 story buildings
[2] Why Wood?.