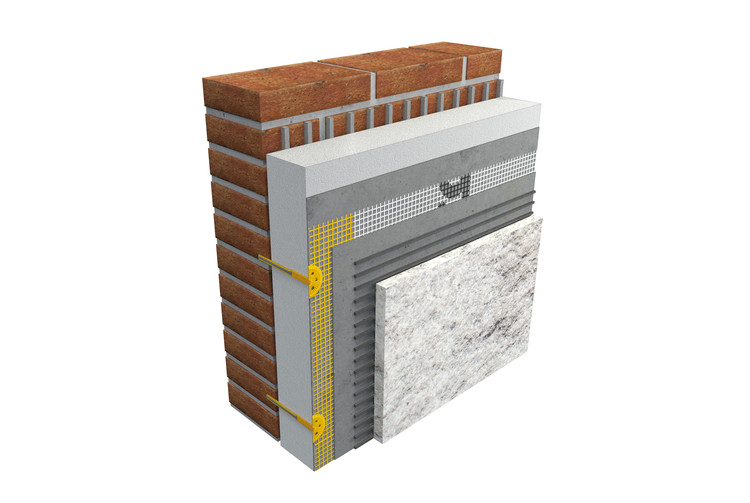
CI (Continuous Insulation System) is an insulated facade system for walls and ventilated slabs that works through the superposition of 5 skins: fixation, insulation, waterproofing (open to the diffusion of the vapor and resistant to impact), and an outer cladding layer.
How are these components installed, and how do they work? Is it a system for new projects or can it be incorporated into existing buildings (retrofit)? How to design an CI correctly for my architecture project? Find these and other answers, below.
Components of a CI
Fixation for Insulating Material
It is usually composed of adhesive mortar. In some cases, mechanical fixings are added, especially if the project has large wind suctions or if a very heavy coating has been placed.
StoTherm | StoTherm Silt
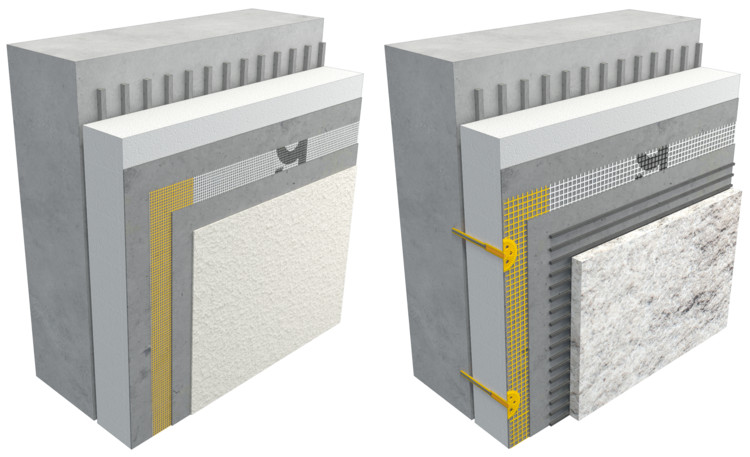
Insulation Material
It depends on the choice of the client and the specific needs of the project. There are a large number of insulators on the market, but the most commonly used are EPS, XPS, Mineral Wool, Insulation Materials derived from Wood, Rigid Silicate Foams, Phenolic Foams, among others.
EPS | EPS Graphite
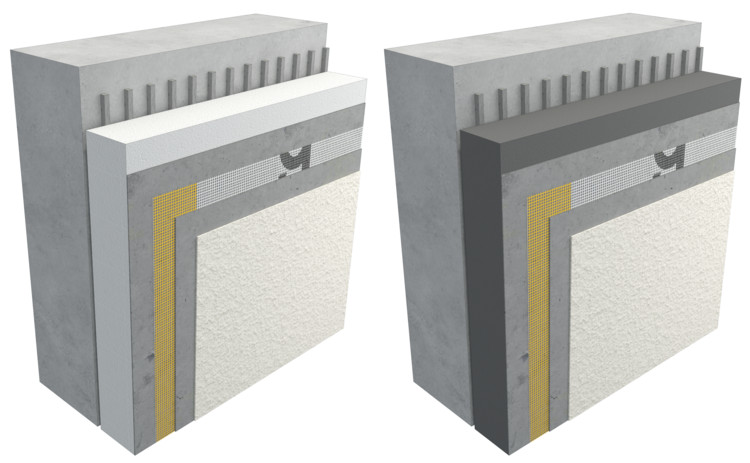
Rock Wool | Wood Wool
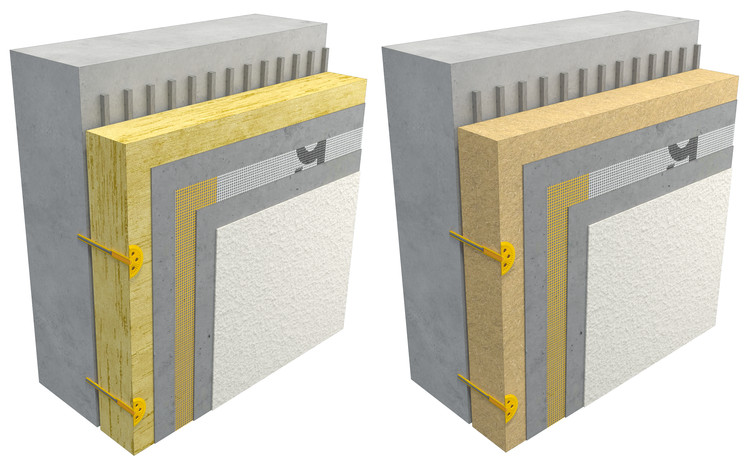
Mineral Foam | Phenolic Foam
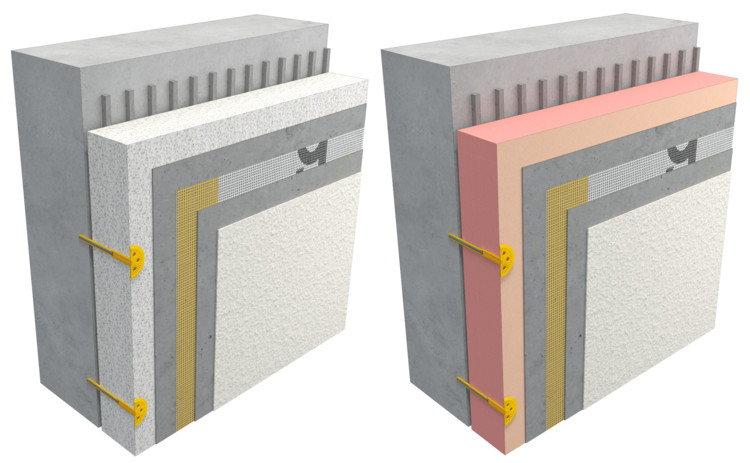
Base layer of mortar with polymers + reinforcement mesh
The base layer, as determined by the European Union, works as waterproofing liquid and a vapor permeable water, while the reinforcement mesh allows the system to properly resist impacts, weather conditions, and other external stimuli.
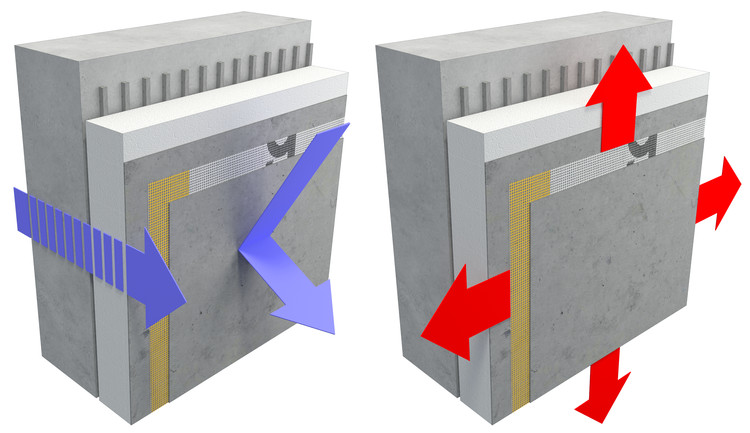
Cladding
It's the final layer and is visible from the outside. It can be chosen from a wide spectrum of coatings, paints, and other finishes.
On what surfaces can it be applied?
These systems originally arose to improve existing buildings, so they can be applied on any type of surface: masonry walls, concrete (coated or not), prefabricated systems, lightweight wooden or metal partitions, OSB, fiber cement, gypsum boards for exteriors, among others. Being that it is composed of air, it is a lightweight system that doesn't add extra weight.
It's important to note that in developed markets, this type of system has been regulated so that it's a single manufacturer delivering the complete product. Thus, the performance will correspond to a single provider.
Concrete | Baumax Prefabricated Partitions | SIP Panel
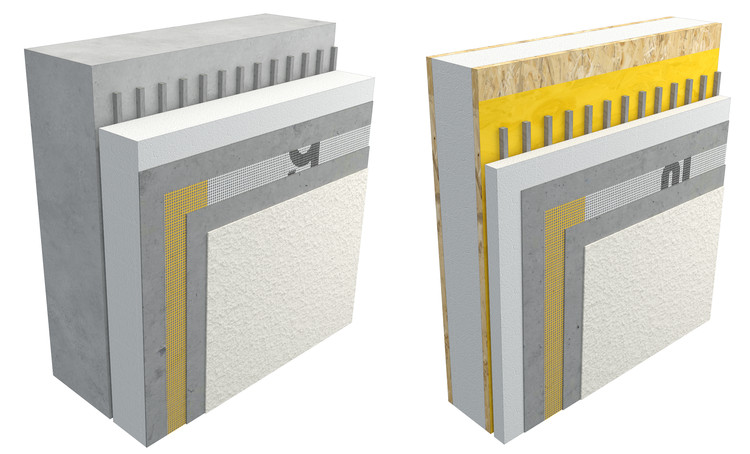
Fiber Cement Lightweight Partition | OSB plate | Exterior Gypsum Board
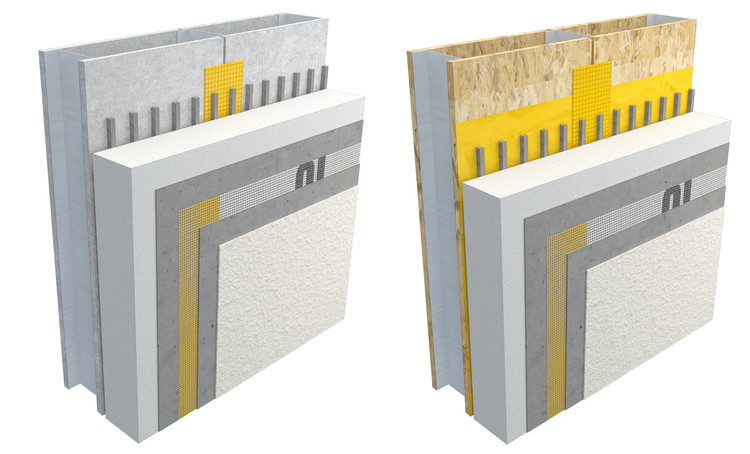
Masonry | Existing wall coated
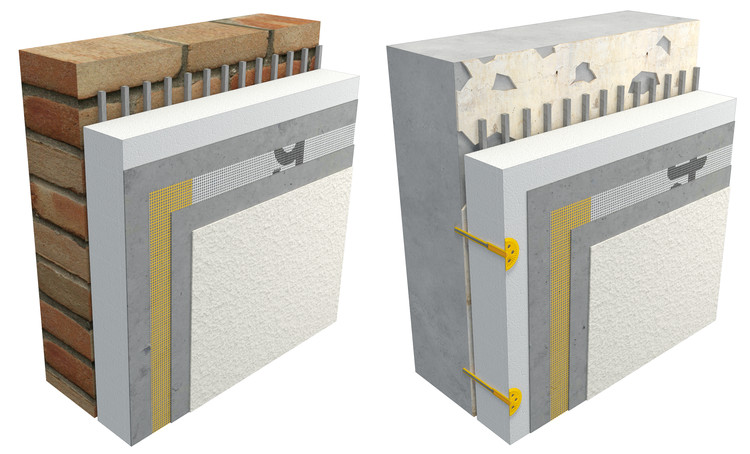
Prefabricated EPS (ICF or Exacta)
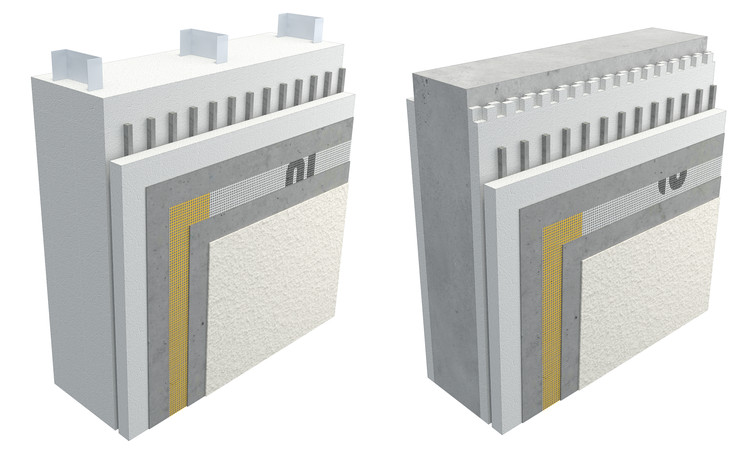
Design Considerations
1. Start by asking: How much do I want to isolate?
Before designing an CI system, we must answer the following questions: Was an energy analysis of the project carried out? Is there a U value (thermal transmittance) that must be achieved? Is it a project developed under the air pollution program, with stricter U values? If our CI system is designed to achieve the U value required by the project, we can rest assured of its thermal behavior in the future.
2. Determine how wide the system is based on your specific conditions
The width of the system is varied and can range from 2.5 cm to 20 cm, the most common being a width of 8 cm. First, the envelope must be defined: what surface will separate the conditioned spaces from the non-conditioned ones? Is it a public building that faces the street? What impact risks will it have on the system? It's not the same to design a CI under an eave in a 3rd floor than one that is at street level or exposed to weather conditions (rain, hail, direct sun, wind, others).
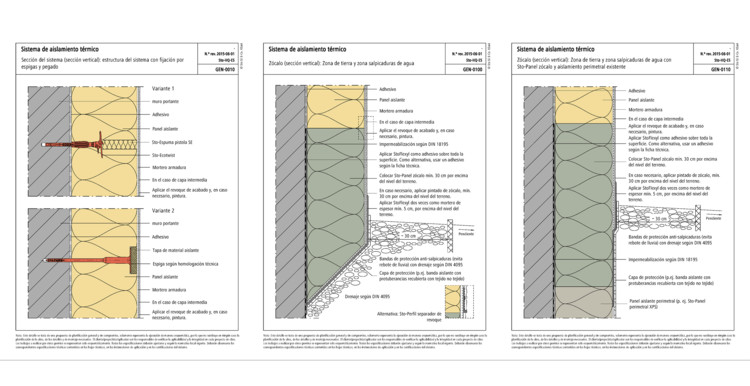
3. Choose the insulating material according to the project's needs
As previously stated, you cannot design a CI for a standard wall or a ventilated slab in the same manner as a site with water damage. Different insulating solutions can be mixed in the same project, depending on the area where the system is located. Also, the U values will be different if the CI is applied to a wall or a ventilated slab.
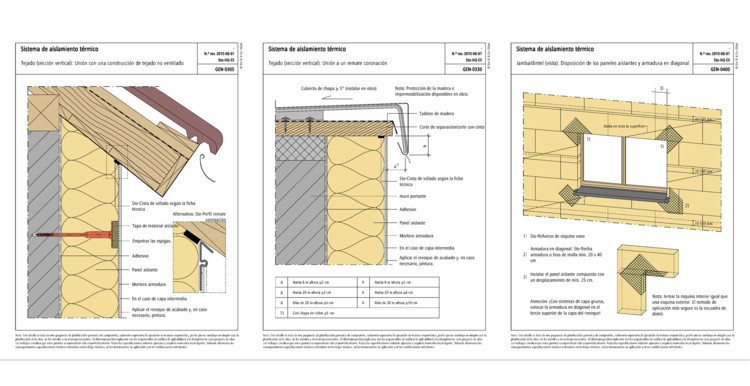
4. Define the connection between the CI and the insulation systems of the roof, the base, windows, and others
As it's not a system for roofs or submurations, CI forces us to determine how our wall insulation will be connected to the roof insulation: should I wrap everything and fit the CI in the roof insulation system? Or can it be applied to the wall without the need for splicing? As for the base, we must also define how far the insulation will go, and how it will be connected to the floors' insulation.
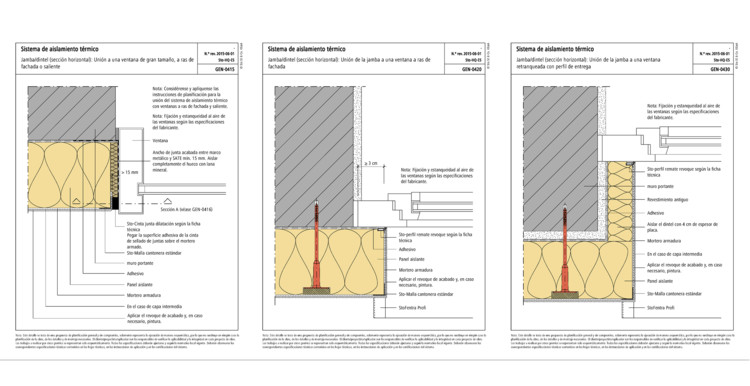
5. Resolve the connection between the CI and the elements that "interrupt" the system
In addition to the roof and the base, all those elements that could "interrupt" the system must be identified and resolved: doors, windows, lighting, and others. In existing buildings, all these pre-existences must be considered, and at the same time the substrate on which the system will be applied must be studied: is it a stucco or paint that is easily peeled off? Do you need to scrape? Can I simply use a primer that improves the adhesion between the wall and the system?
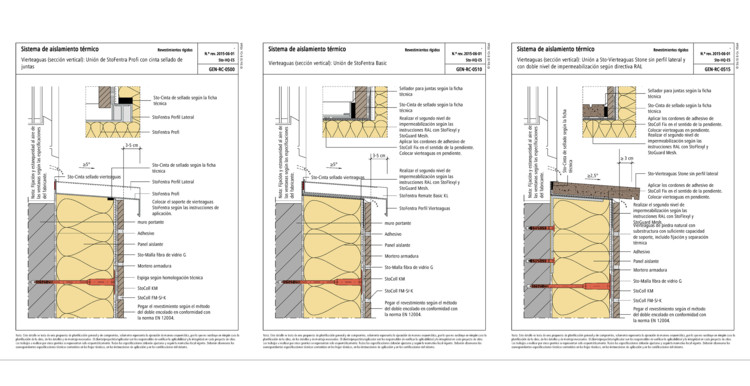
6. Look for advice and analyze the technical characteristics of the CI offered
CI is not a painting; It's a solution that has a certain volume and, therefore, requires professional advice to ensure its proper functioning. In this sense, it's important to understand the technical characteristics of the product, and require a set of instructions that explains everything we need to know before applying it to our project.
* CI systems are also known as EIFS (Exterior Insulation Finish Systems), SATE (External Thermal Insulation System), EWIS (External Wall Insulation System), ETICS (External Wall Insulation Composite System), WDVS (Wärmedämmverbund System) or Thermohaut ("Thermal Skin").
The images in this article have been developed by Nicolás Schultz, STO Chile Product Manager.