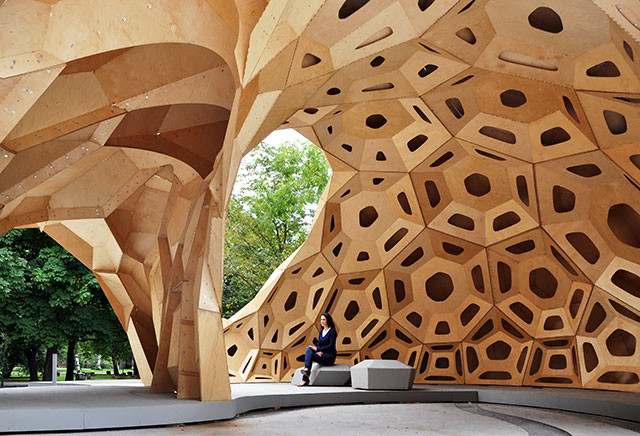
In this article, originally appearing on the Australian Design Review as "Tolerance and Customisation: a Question of Value", Michael Parsons argues that the complex forms made possible by digital fabrication may soon be victims of their own popularity, losing their intrinsic value as they become more common and the skill required to make them decreases.
The idea of tolerance in architecture has become a popular point of discussion due to the recent mainstreaming of digital fabrication. The improvements in digital fabrication methods are allowing for two major advancements: firstly, the idea of reducing the tolerance required in construction to a minimum (and ultimately zero) and secondly, mass customisation as a physical reality. Digital fabrication has made the broad-brushstroke approach to fabrication tolerance obsolete and now allows for unique elements and tolerance specific to each element. The accuracy that digital fabrication affords the designer, allows for the creation of more complex forms with greater ease and control. So far, this has had great and far reaching implications for design.
Read on to find out how this ease of form-making could diminish the success of complex forms.
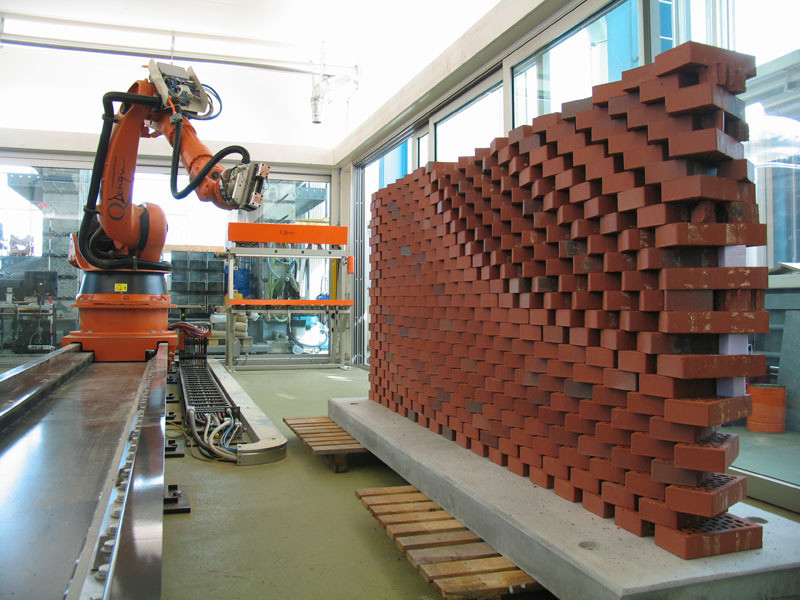
The Abedian School of Architecture, Bond University, is currently installing its first robotic industrial arm, thereby joining the growing number of Australian architecture schools investing in advanced manufacturing processes. The continued mainstreaming of advanced digital fabrication processes such as, 3D printing, CNC milling, laser-cutting and robotic manufacturing in architecture schools, affords students the luxury of creating designs using these tools. Suddenly they have the freedom to explore digital design and manifest these digital designs physically, regardless of the complexity.
These processes have narrowed the gap between digital representation and the physical outcome. Now students can work in a digital world of infinitely thin lines and surfaces and are still able to manufacture physical products without much consideration for the modification of the digital model to account for physical constraints and tolerance.
The word ‘tolerance’ is commonly venerated as an ever-present guide to realise a design. It is seen as an acceptable level of difference between the represented ideal and the physical reality. The physical reality of a design is influenced by a vast variety of factors including, and possibly most importantly, the manufacturing process used, which accounts for the continual use of generalised tolerances. Although professionals may, on occasion, have access to digital fabrication tools, not all practitioners specifically design with digital fabrication in mind.
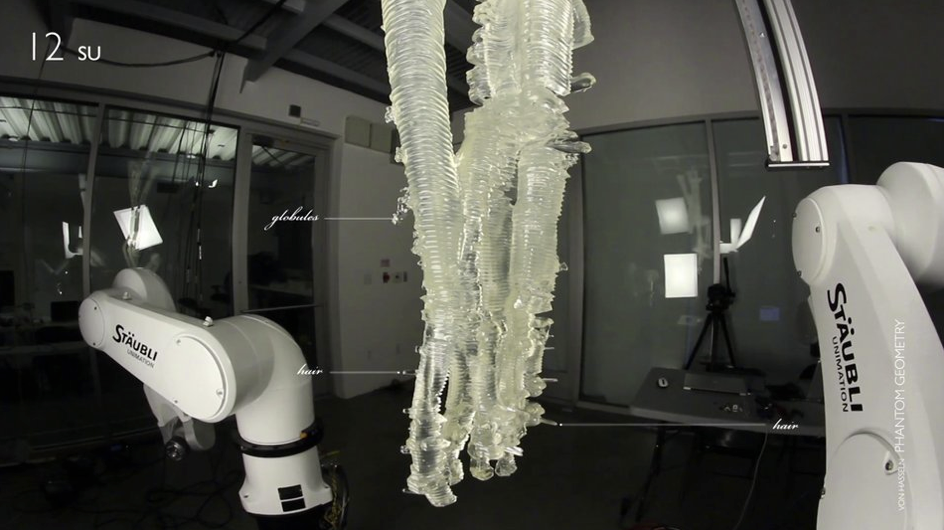
Students, unlike practitioners, are not restricted and as a result produce complex designs for a future we have not yet reached. Therefore, I think it is important to look at the implications that operating at zero required tolerance would have on the future of design. Complex, organic or algorithmic designs are undoubtedly evocative and captivating, but there may be a larger ethical consideration to be taken into account.
As fabrication technology tends towards requiring zero tolerance and develops more refined abilities to manufacture complex geometry, social tolerance for complex design will most likely increase. As is the case for many new technologies, the work of the early adopters stands out as avant-garde, but by the time late adopters are using the technology, the work it produces has become largely accepted and sometimes even the norm. Suddenly what was a unique work one year, is homogenous the next. With increased access to digital fabrication, comes a propensity to over-use or at least to use these methods without consideration.
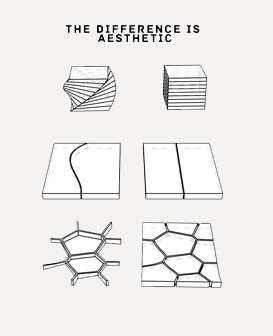
Let’s look at a few examples. Firstly, in computation, the use of the Voronoi Diagram has become so commonplace that it no longer demonstrates any level of skill, quite the opposite in fact. The use of the Voronoi Diagram now requires a strong rational justification because its aesthetic appeal has become devalued by overuse. Another example can be the comparison between a simple 3D-printed cube and a twisted counterpart. Both cubes require the same number of print layers and similar print time; the only real difference is aesthetic.
A third example can be the use of a robotic arm to cut two lines, one dead straight and the other with non-uniform curves. A robotic arm does not know the difference between the cuts other than the fraction longer the curved line will take to cut. Once again, the only real difference is aesthetic. In the past, there was a difference in both skill of fabrication and aesthetic design; now there is simply an ever-decreasing skill in fabrication.
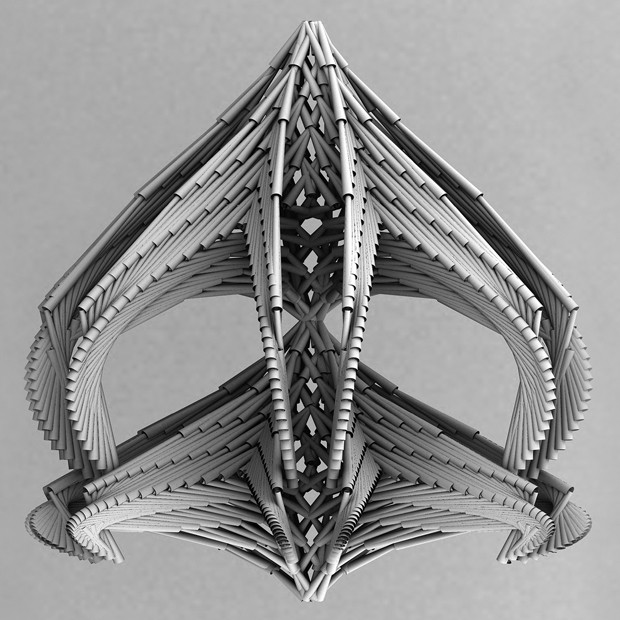
As the skill in achieving complex forms decreases, so does our societal value of complex formal outcomes. Maybe we need to revaluate our perception of difference, in other words our tolerance for complex design. We need to consider that what were two very different outcomes in the past are now only differentiated by one factor, aesthetics and not skill.
Is a blue cube really different to a red cube, if you do not privilege aesthetics? This is where the true issue of digital design and fabrication lies. What distinguishes one work of digital fabrication from the rest? What gives the work significance now that complexity is no longer intrinsically valuable? Students should not hide behind captivating forms and instead require stronger and stronger justification for their work.
As digital fabrication advances towards its goal of requiring zero tolerance, social tolerance will increase and so will society’s perception of homogeneity. Digital fabrication is devaluing itself through overuse and therefore it becomes the responsibility of the designer, and particularly design students, to reintroduce value into a design by synthesising multiple and complementary sources in a way that is unique and innovative. The challenge for students is not achieving technical or digital brilliance, but rather employing these mainstream tools to achieve architectural brilliance.