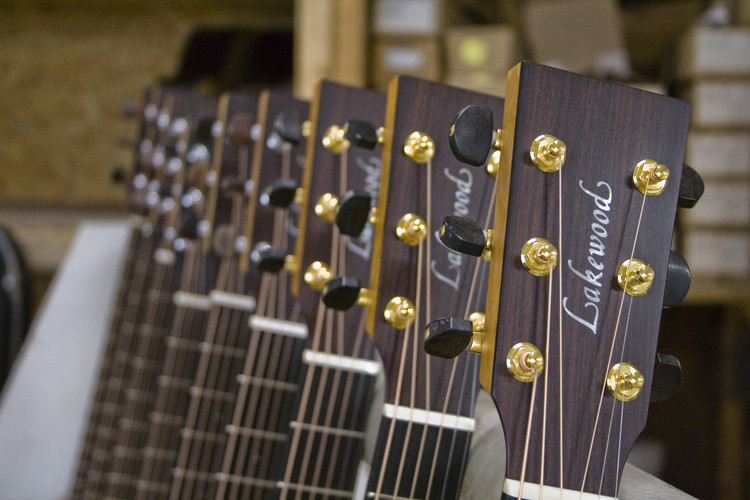
In the middle of Europe, Martin Seeliger has been building acoustic guitars for 30 years now. The success of the Lakewood factory proves that with good old craft, transported to the modern era, you can build a global brand. See how EGGER interprets craftsmanship with their handcrafted style in their forthcoming decorative collection.
On average about 5 guitars leave the Lakewood manufacturing plant in Giessen (DE) a day and make their way to music shops around the world. Trend: a steady rise. "We drive cautious growth because there is a certain compromise we never want to make: the quality of the instruments and the materials that we use," says founder Martin Seeliger.
In 1986 Martin Seeliger, then 28 years old and a freshly qualified luthier, let his finger circle on a USA map. He needed a catchy name for his instruments: acoustic guitars, as heard in pop songs from the Beatles to Cat Stevens to Bruce Springsteen. At the time they were mostly built by the big American players such as Martin or Gibson. But what do you name a company from tranquil Giessen who is trying to enter an American-dominated market? Seeliger's finger carried on circling until it came to rest on the name of a small town on Lake Erie: Lakewood.
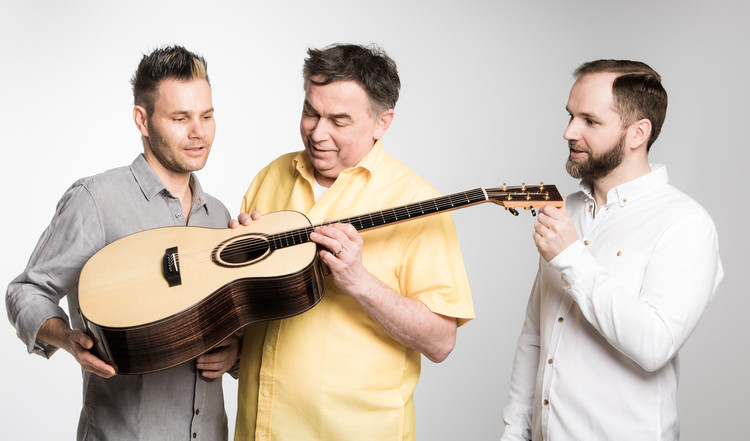
In American professional forums, players place it on a level with the highly respected US instrument manufacturers like Santa Cruz or Collings. They preserve the spirit of the old style American steel string guitar, but update it with innovative ideas and methods to take it into the modern age. Martin Seeliger has also introduced ever more mechanical help into his production process over time.
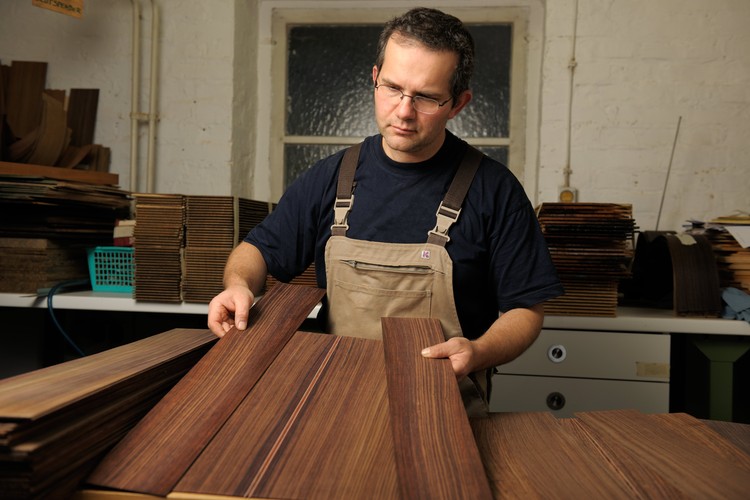
We are quite old fashioned at heart, but there is no false romanticism here. Where a computer-controlled milling machine does the job more accurately and better, we use that. But, at the end of the day, building a guitar, tuning it and achieving a certain sound, remains an artisanal process - Martin Seeliger.
Eighteen people work at Lakewood, amongst whom fourteen guitar builders. Almost all the separate components of a guitar are prepared here onsite. Shelves full of precious tone bearing woods are ready for use. From Alpine spruce and cedar for the sound board to rosewood from India and mahogany from Ghana for the body to a pitch-black ebony for the fingerboard. The wood must be stored, some of it for decades, until it is ready for use in construction.
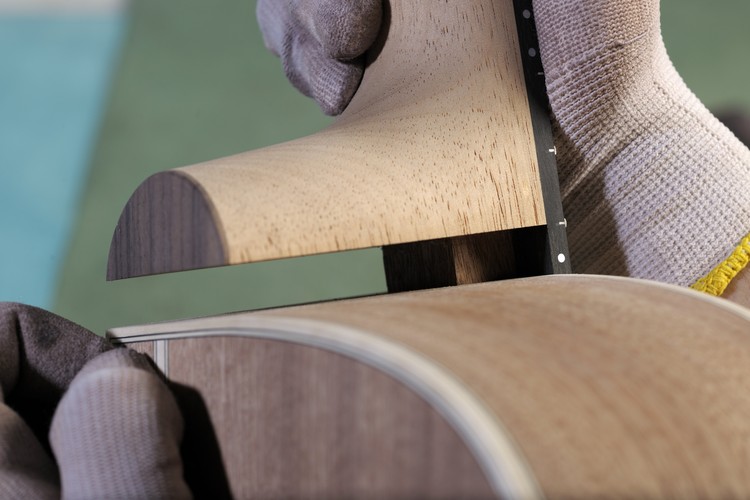
The large selection is necessary. Hardly a single Lakewood looks like another, says Martin Seeliger: "We build a lot of custom shop guitars. In other words, the customer can specify how they want their guitar to look. We increasingly use materials that have so far not been part of traditional construction methods. Elm and plum, for example.” The reason for this is clear. Tropical wood is becoming harder to source. Lakewood himself only buys wood with a certificate of origin.
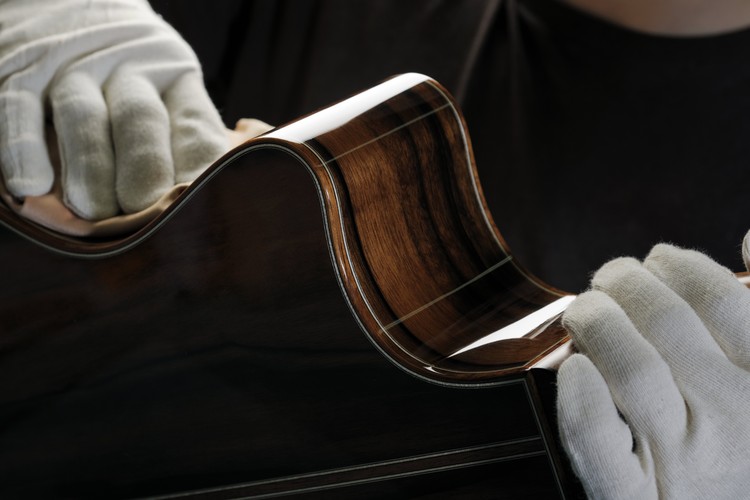
Before the guitars are assembled, they have been painted and polished one last time. In the fingerboards now sit polished frets, glistening in the light. In a large stand, the finished instruments rest, waiting for the final ritual. The boss himself looks carefully at every guitar before shipment to check whether it is perfect. And how does a Lakewood sound? It's a modern sound. Bright and with an accentuated bass. Balanced - but never boring. It is perfection in instrument-making. An old craft that has made it into the modern age. Steel strings at the highest level - from Central Europe.
EGGER, a supplier of wood-based materials, pays tribute to the art of instrument building in its forthcoming decorative range. Deeply brushed wood reproductions through to sandblasted surfaces display the natural character of the materials. The artisanal nature of the material reproductions ensure a high level of authenticity for our metal, brushed and leather textures.
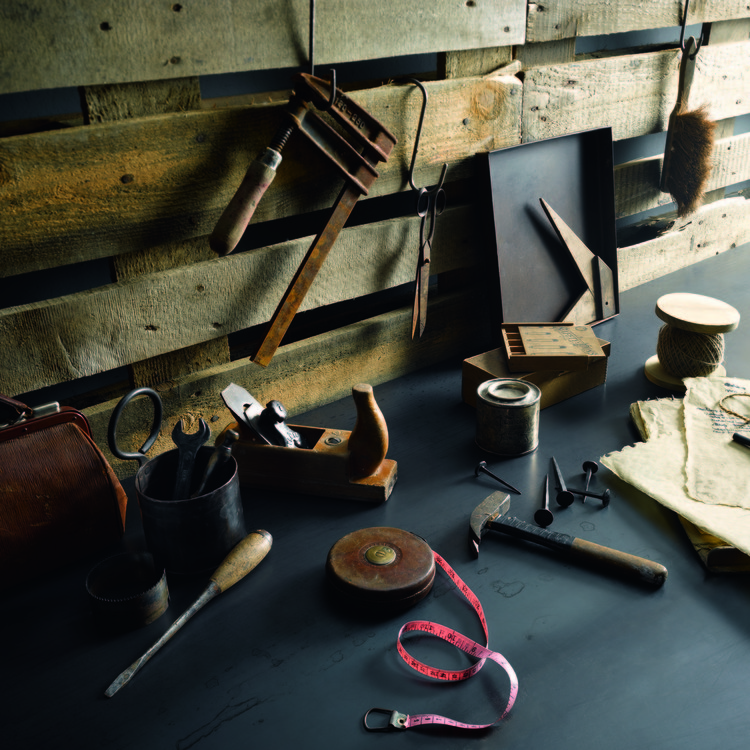
The designs in EGGER's handcrafted style collection are inspired by the small-scale processing inherent in handcrafted surfaces.