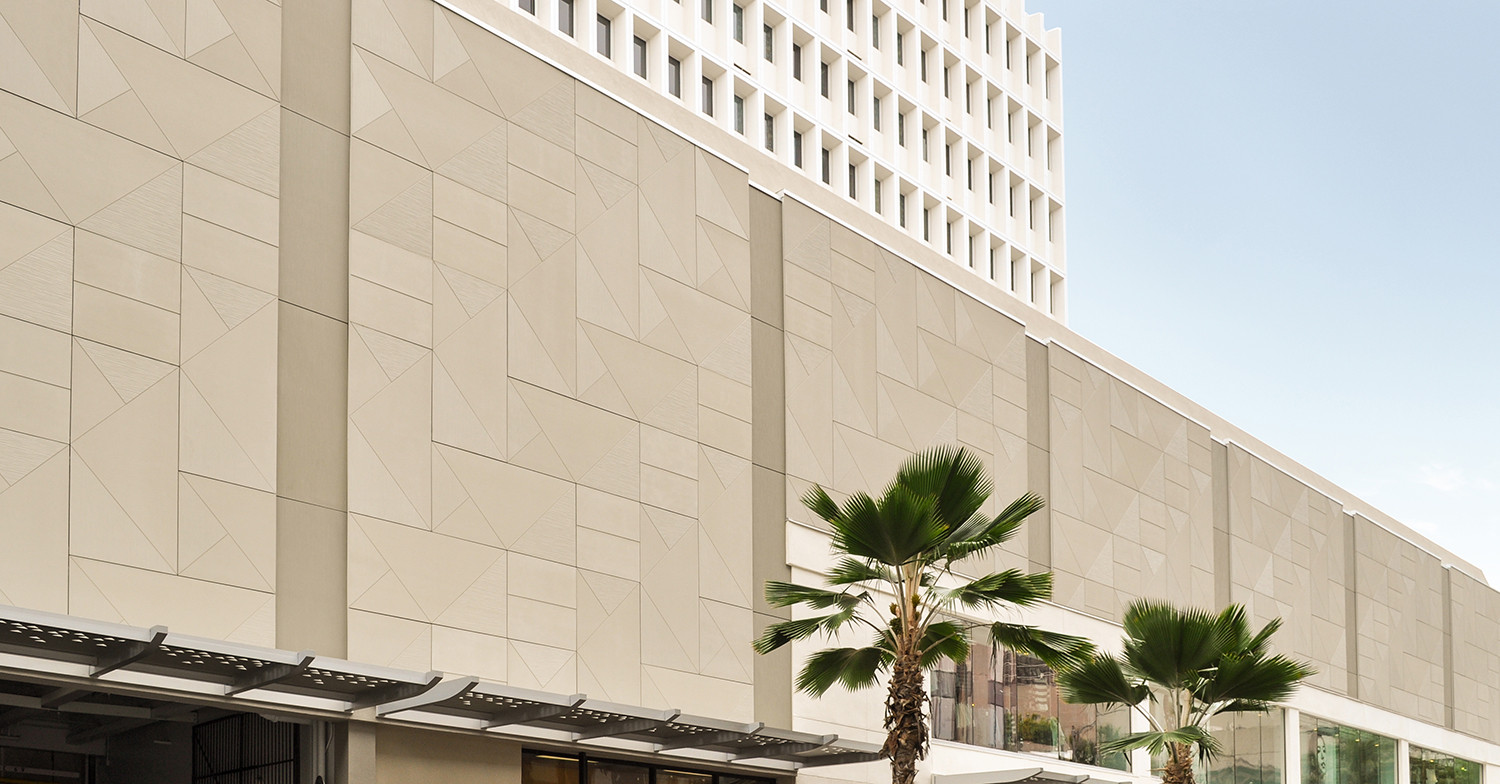
Since the beginning of the Modernist era a century ago, concrete has been appreciated by architects for its strength, versatility and sculptural potential. For many countries, concrete played a key role in their recovery from the Second World War, and in their continued modernization during the second half of the 20th century. But in recent years - while it is still as widely-used as ever - concrete has fallen on something of an image problem, with criticisms of its environmental impact and its aesthetic appearance becoming commonplace.
That hasn't stopped some companies continuing to innovate with concrete. Among these companies is TAKTL, a facade panel designer and manufacturer that works exclusively with Ultra High Performance Concrete (UHPC). To find out what UHPC can offer to architecture, ArchDaily spoke to TAKTL about the potential of this material, and the future of concrete construction.

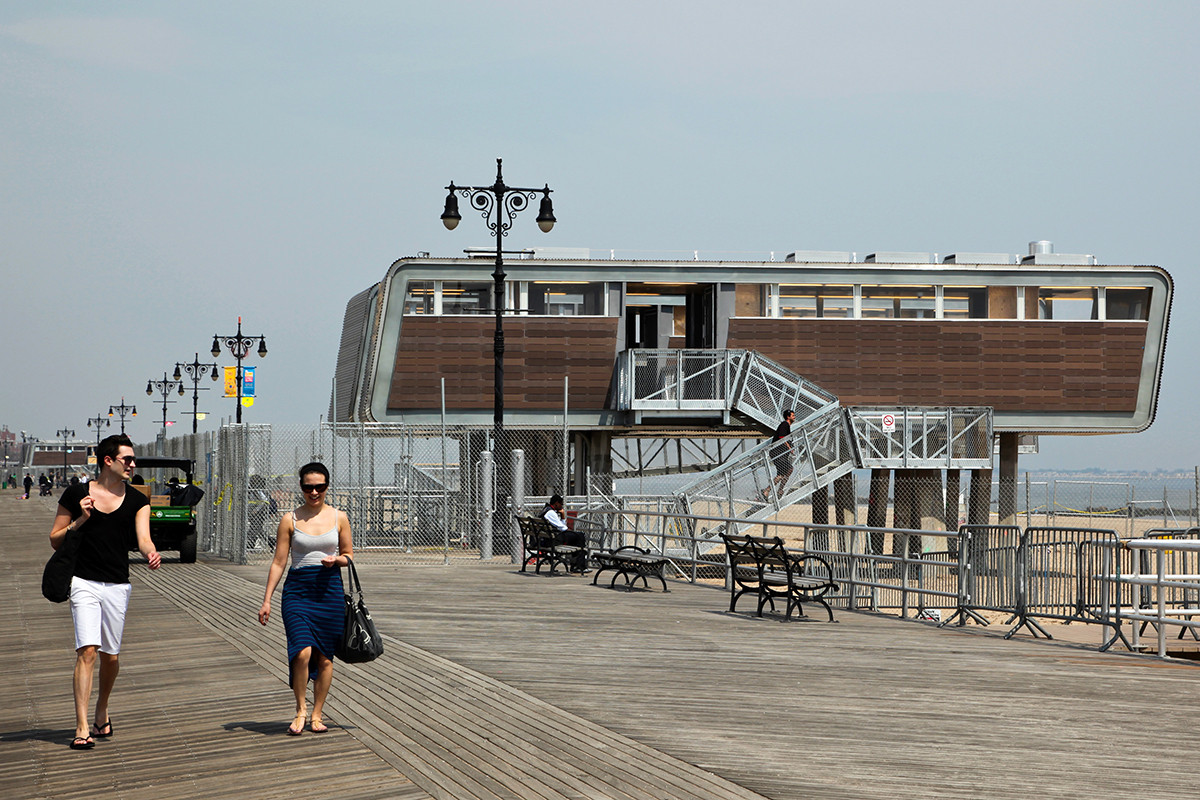
ArchDaily: Concrete often gets a bad reception due to its environmental effects and due to its connection to monolithic failed projects of the post-war years. What advantages do UHPC panels have over these other forms of concrete construction?
TAKTL: Let’s address environmental impact first. The bad rap is primarily because cement, one of the main ingredients of concrete, is so energy and CO2 intensive to produce. Although UHPC starts with a lower percentage of cement in its formulation, the real savings in environmental impact is driven by just needing a lot less of it to accomplish the same goal. UHPC is so much stronger than conventional concrete, that TAKTL facade elements can be significantly thinner and lighter than traditional precast or cast-in-place concrete. So from an environmental impact standpoint, because the envelope components are lighter, we can drive reductions back through the primary building structure and also replace weight with thermal performance (by replacing dead weight with insulation). Further, because we are a vertically integrated manufacturer, in addition to better quality control we also can control waste, energy consumption and emissions, and better analyze impacts through the use of LCA modeling and continually improve our process.
Traditional concrete also degrades over time, particularly in freeze thaw conditions due to spalling, cracking, and water and chloride migration through capillary action to the steel reinforcements. By contrast, UHPC is created with a very tightly-packed density of extremely small particles, carefully calibrated and mixed in a specific sequence, to produce strong molecular bonds that result not only in exceptionally high flexural strength - but it also virtually eliminates the chloride migration and water suction that cause freeze-thaw degradation and corrosion in traditional concrete structures and GFRC elements. Although it is possible to reinforce TAKTL with steel, the primary reinforcing we use is AR Glass in a variety of types and forms. Beyond basic material performance differences, we can also point to our manufacturing process that is quality certified to consistently produce facade elements that exceed ASTM standards. In this type of factory setting tolerances in every step - from automated dosing and mixing of raw materials, through processing panels utilizing CNC 5-axis bridge saws, and automated finishing equipment - are just able to be much tighter than what is possible at a project site or even in most precast facilities.
TAKTL UHPC facade elements are made without steel reinforcement and are easily installed with continuous insulation and ventilated wall assemblies, which are increasingly being mandated by regional building codes. They are resistant to salts and carbonation, giving an extremely long life span, and offer superior freeze/thaw performance, a higher strength to weight ratio, longer spans between anchors (reducing substructure and installation costs).
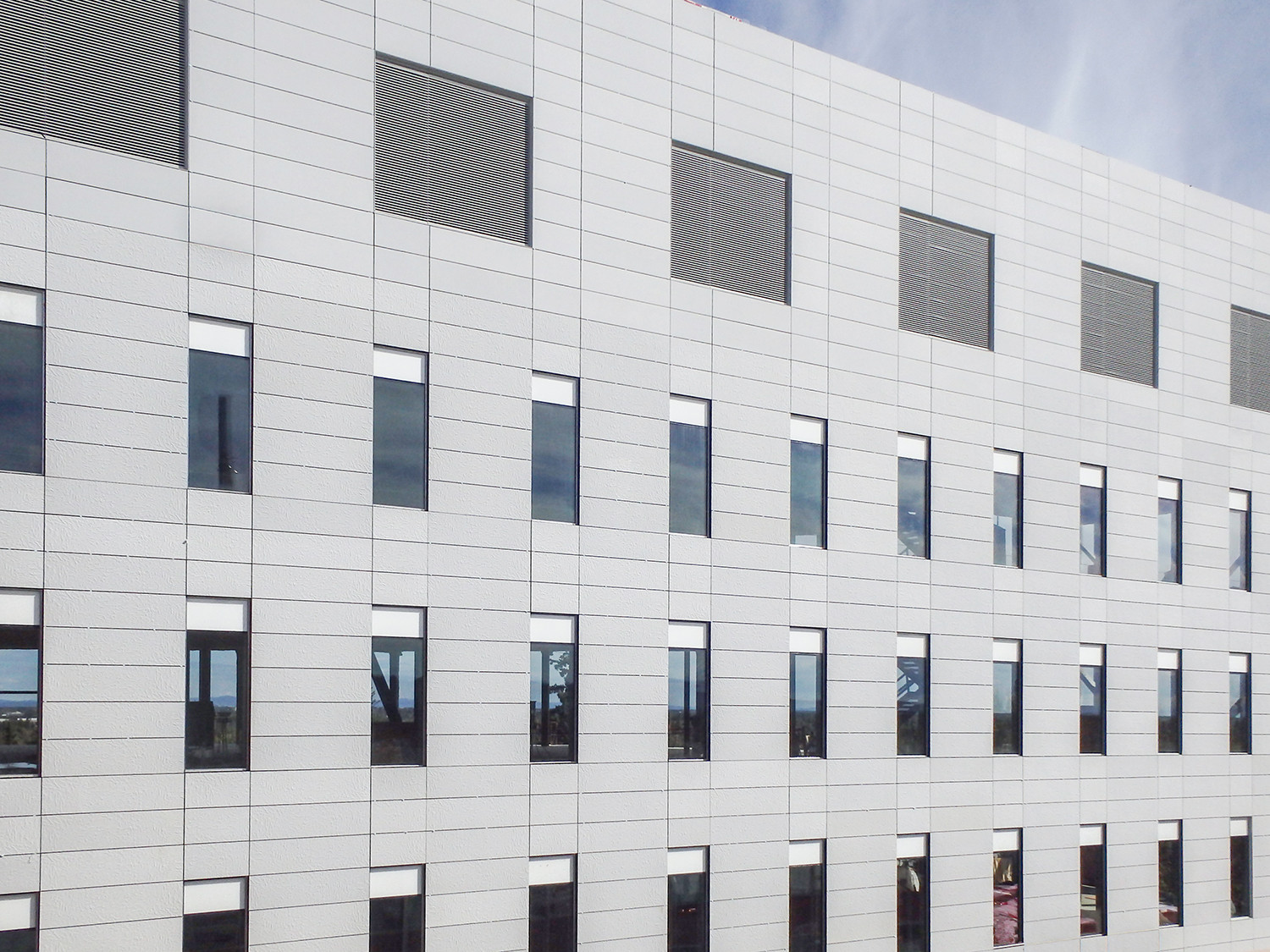
AD: You are the first company to work with the whole process, from the development of UHPC formulas, to the design of panel molds, to the creation of the panels themselves. What advantages does this provide - to practical implications such as cost but also to the expressive potential that your products can offer architects?
TAKTL: First of all, UHPC is an exacting high tech material that requires control of many manufacturing and environmental variables to obtain the best aesthetic and strength results. This is our entire business. It is all we’ve done beginning with the years of basic research and development through our continually expanding production process and design capability. We understand how UHPC behaves, what will work, what won’t, and how to achieve the design intent in the best way possible. We are as much product and machine designers as we are mold fabricators and UHPC pre-casters. This allows us to have a very heads-up approach to problem solving and the ability to be more collaborative with architectural designers and installers, since our team encompasses all the related disciplines. Take one piece of the process for instance, such as mold design. There are many factors to consider beyond the obvious: tolerances of the mold materials and fabrication process, ease of de-molding and cycling the mold back into production, durability of the mold, accommodating the impact of material shrinkage on surface design or part geometry, end of life disposition of the mold, to name a few.
On a purely aesthetic level, the very dense microstructure of TAKTL is able to so precisely replicate the pattern and texture of a mold surface that there is very little detail the surface cannot capture.
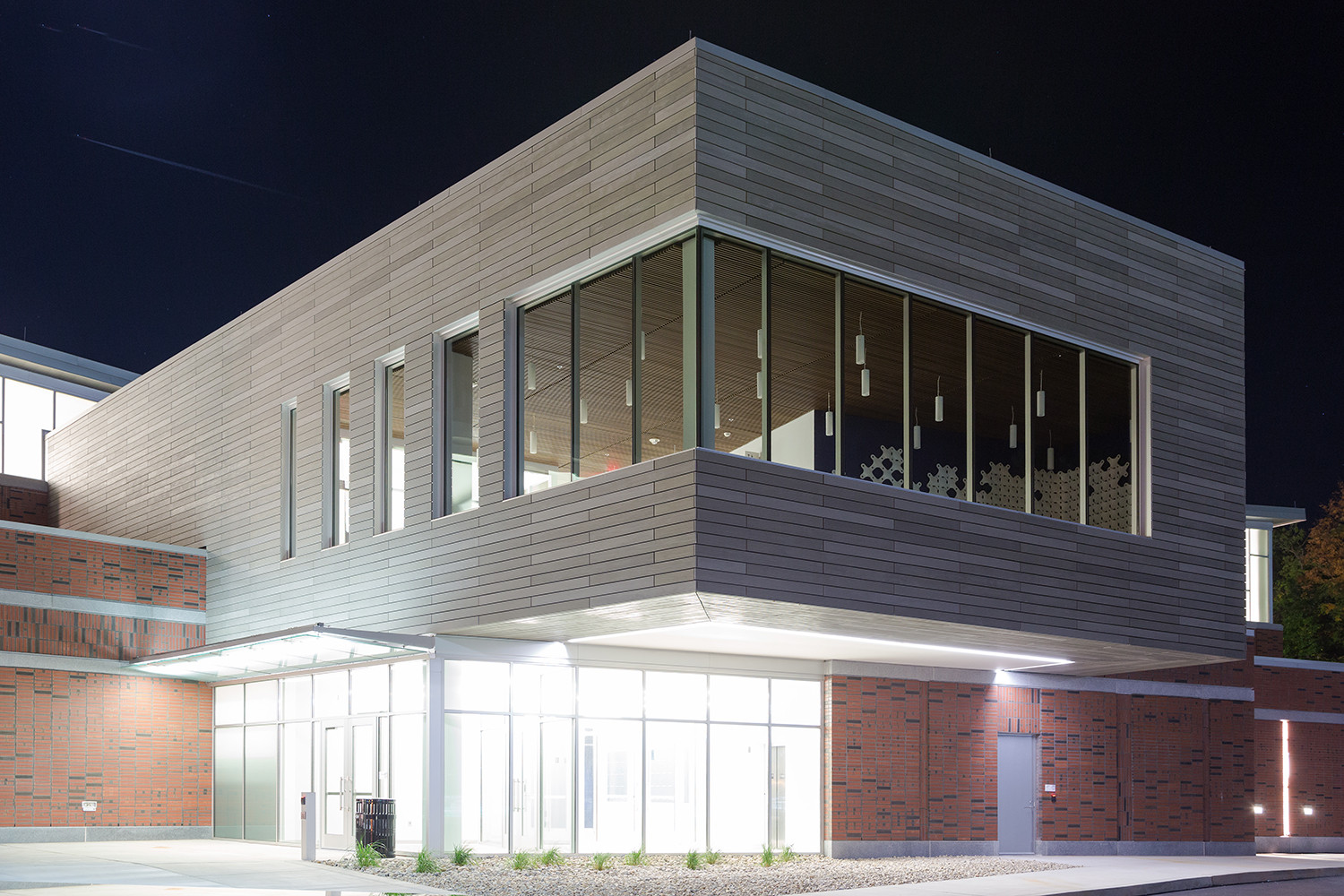
AD: What are the benefits of continuing to push concrete technology? And, what do you think the future of concrete construction will be like?
TAKTL: Interestingly enough, we have recently created a new company, VECTR Research that will be focusing on just that: developing new material formulations, new applications for Ultra High Performance Concrete, and new manufacturing technologies, as well as their points of intersection with other materials and processes in architecture.
We are excited by the interesting things we see possible in the marriage between structure and surface aesthetics. In UHPC, you have a material that is both plastic and permanent, so you have the opportunity to make almost any form you want that will last forever, require very little maintenance, and age gracefully. With continued development of manufacturing technologies, our hope is to make it more accessible because ultimately it will outperform many other materials from an environmental impact, aesthetic, and durability standpoint.
We are actively pushing into applications that can leverage the extreme strength of UHPC - blast mitigation, wind and extreme climate conditions, and other aspects of resilient building design. We’re also currently investigating the question of thermal mass and the location of specific patterns to optimize heat take-up and dissipation.
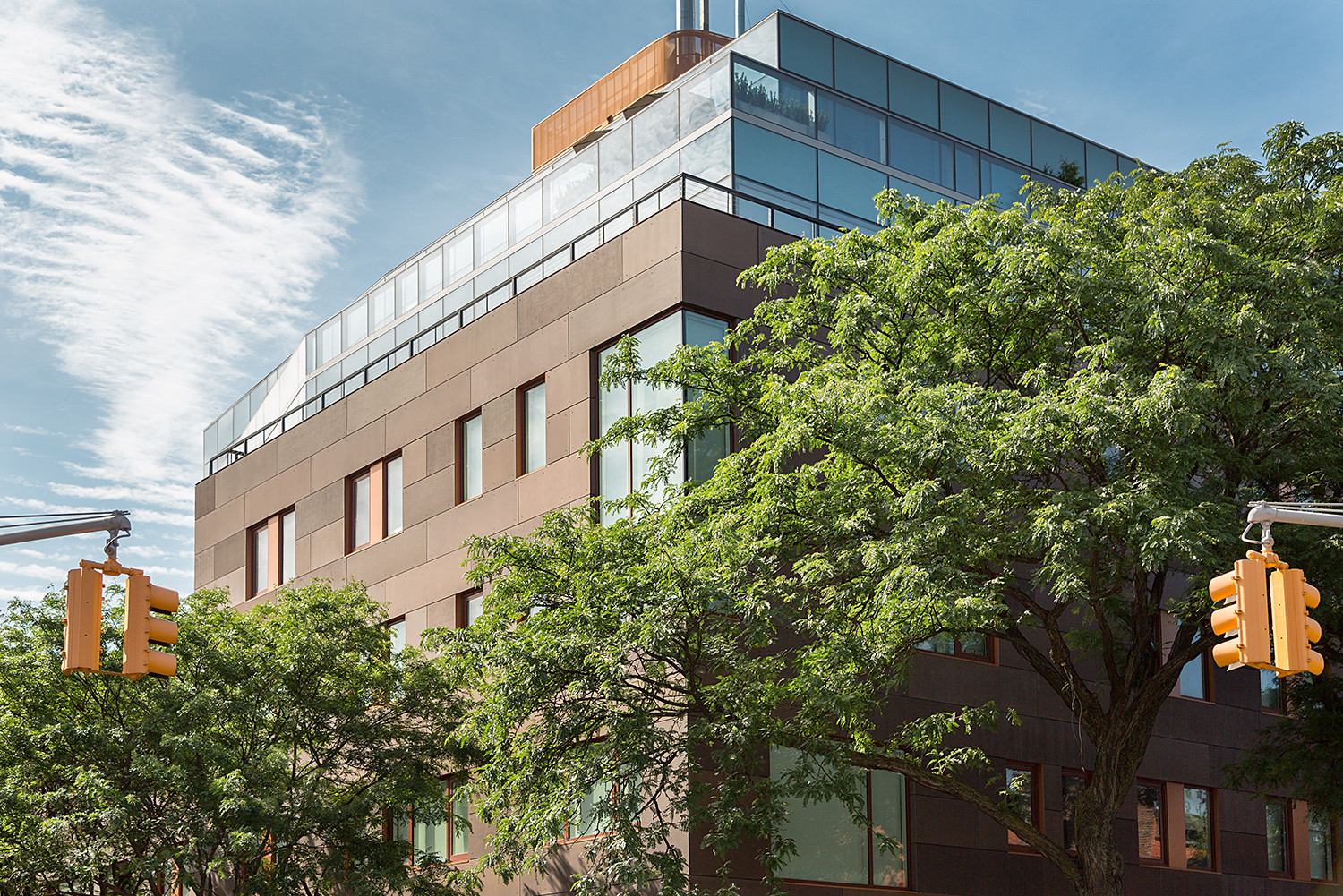
AD: Are there any particular applications of TAKTL panels in buildings which you thought were particularly innovative or interesting?
TAKTL: Quite a few, actually. Here are a few that immediately come to mind:
Extreme Climate: College of Engineering at University of Alaska Fairbanks / NBBJ
Accommodating issues of extreme cold and temperature swings and a very short construction season, NBBJ designed a unitized curtainwall with heavily insulated panels clad in TAKTL. Panels were fabricated in the installer’s factory over the winter and installed quickly during the short summer.
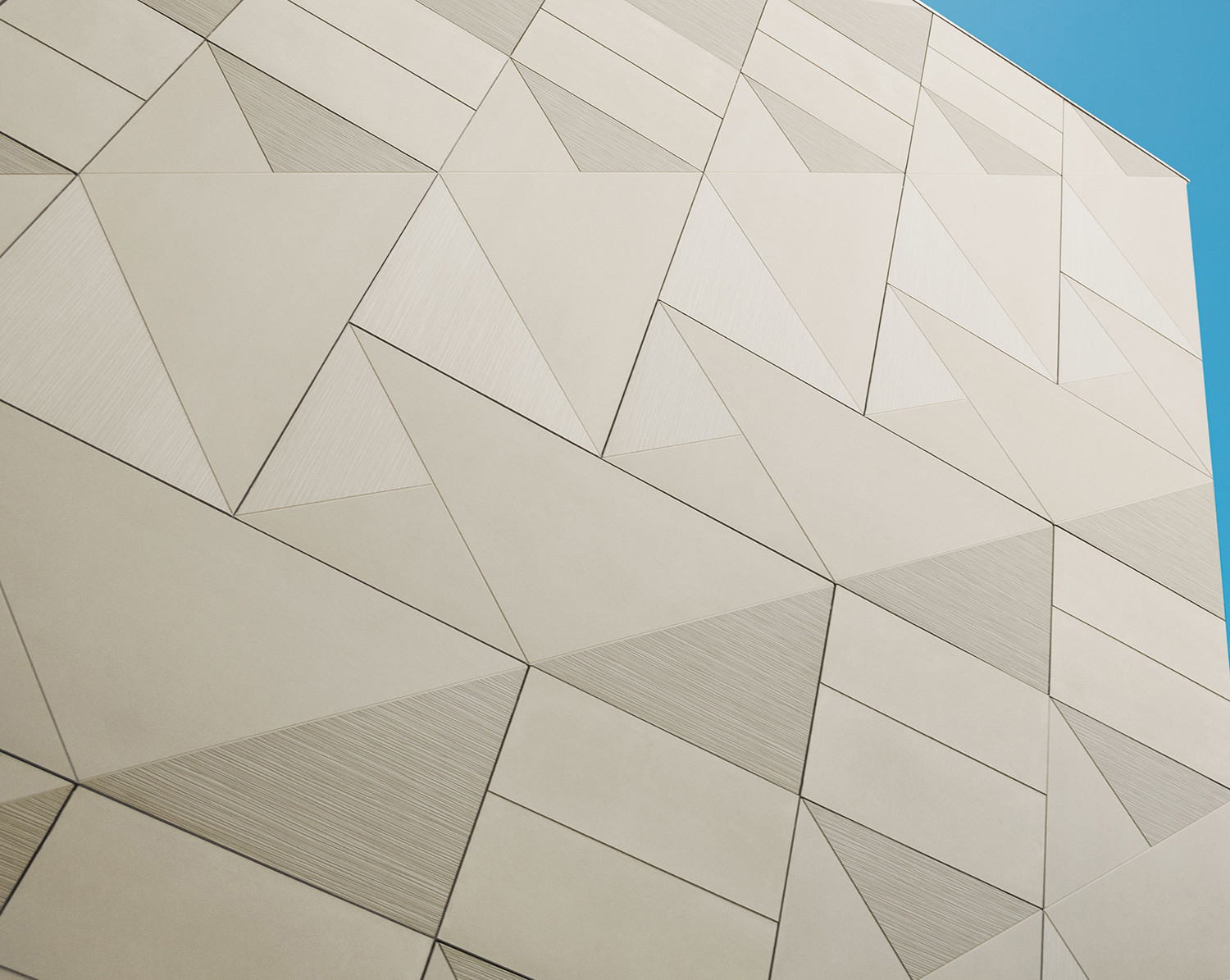
Innovative Use of Texture: Waikiki Business Plaza / MGA Architecture
This was a recladding project in which we were able to cast large panels with multiple textures to regularized the architect’s triangular surface pattern which would have been very difficult and expensive to install as individual parts.
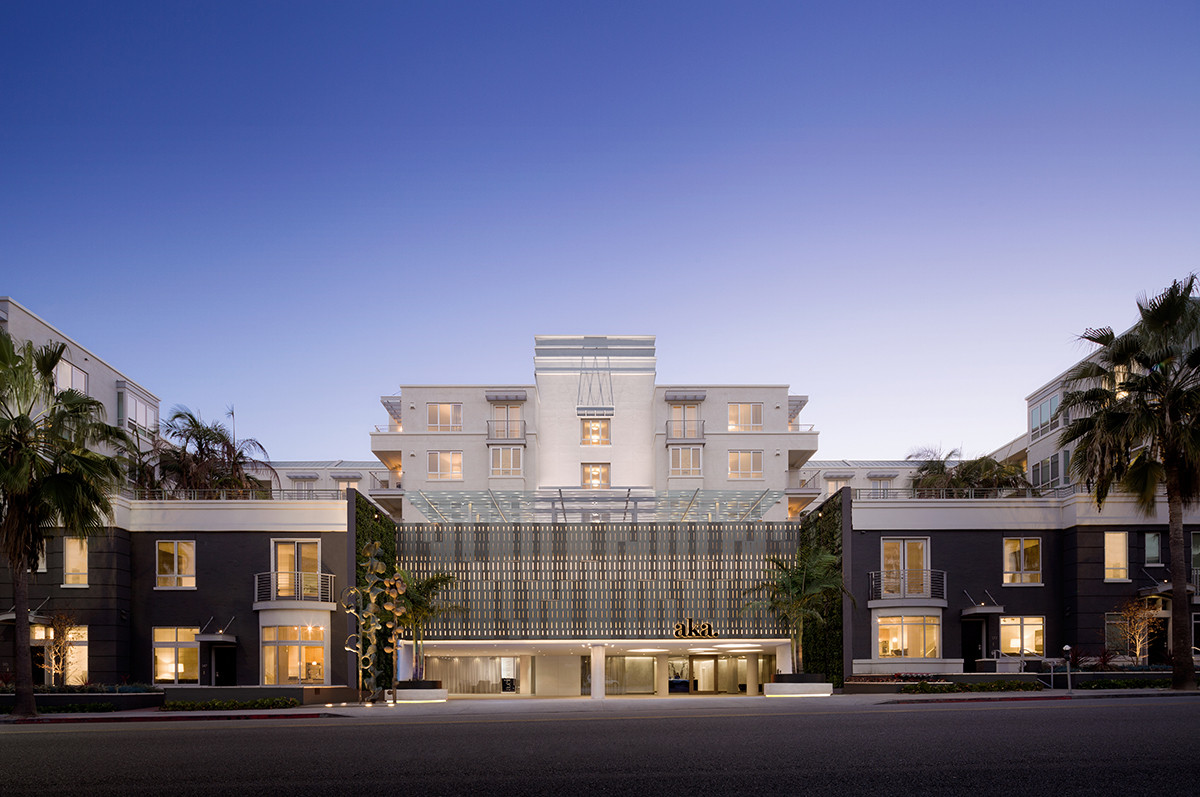
3D Facade Elements and Screens: We have a number of projects underway where the designer has used fins or perforated panels for both building shading and aesthetic value. This direction of combining increased building performance with decorative effect seems to of increasing interest.
Ribbed cast corners: A large project, again still confidential, in which the architect has achieved the substantial look of stone at a fraction of the weight and cost, by designing ribbed corners that are precisely cast with TAKTL and incorporated into a unitized system. This is another great example of collaboration between the architect and TAKTL’s design team.
TAKTL as permanent formwork: We really like the direction several architects have taken with the idea of casting three dimensional UPHC parts that become the permanent formwork for larger structures.
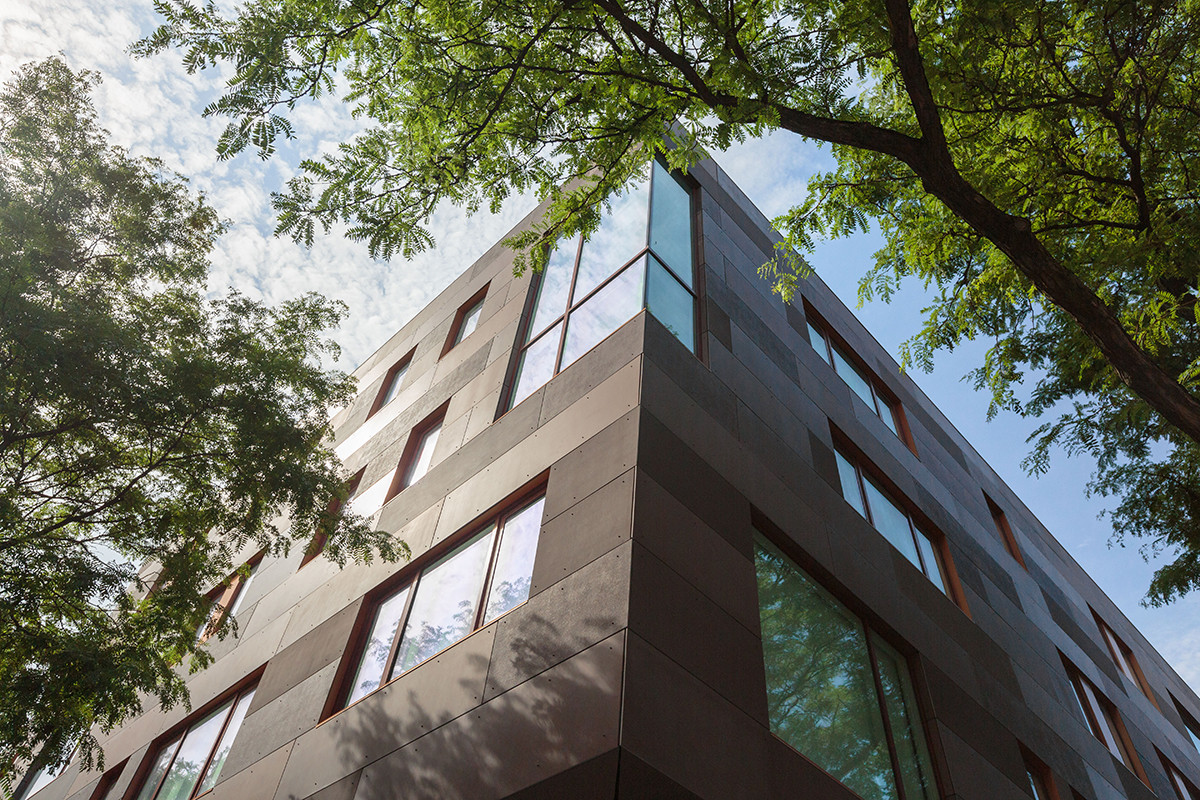
Innovating with Standard TAKTL Panels: Finally, we have some architects who investigated really interesting ways to use the textures and colors in our standard panel lineup and achieved great results: Wake Tech Community College, Sackett Union, NYC Beachfront Restoration, University of Connecticut Basketball Development Center.
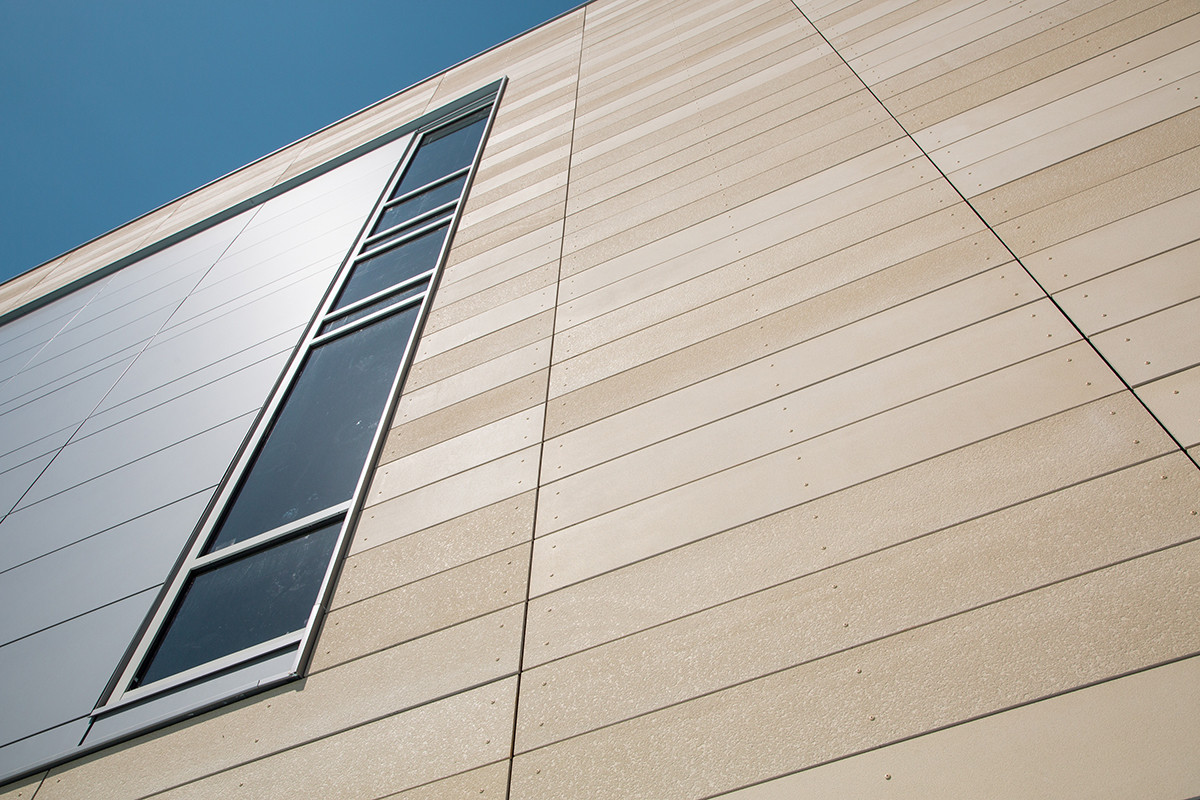
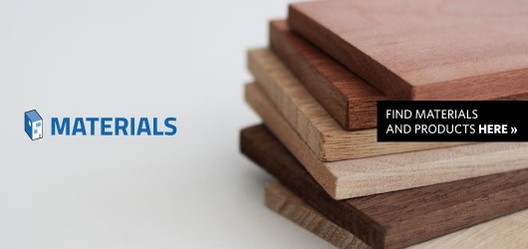