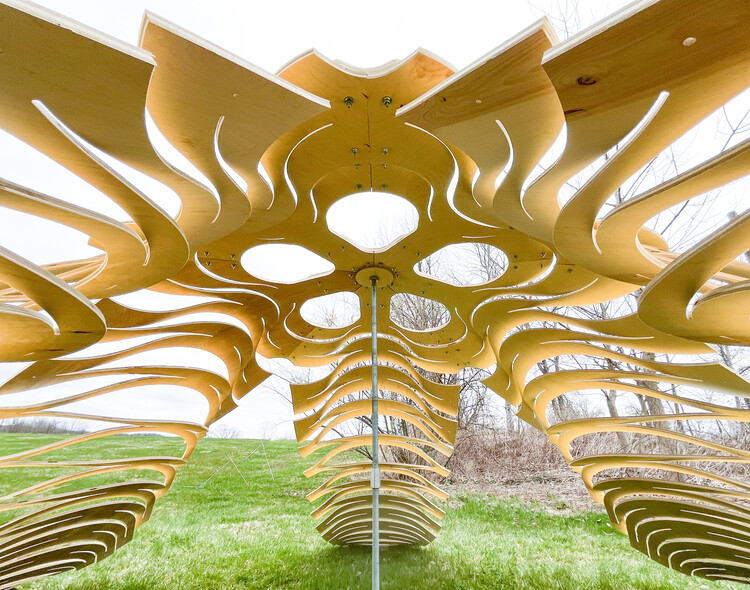
-
Architects: Neal Lucas Hitch
- Area: 200 ft²
- Year: 2024
-
Photographs:Thanut “Hint” Sakdanaraseth
-
Lead Architect: Neal Lucas Hitch
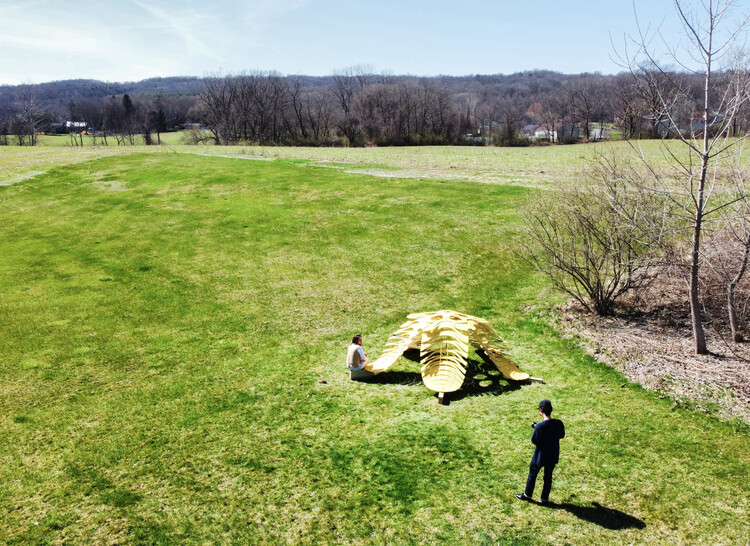
Text description provided by the architects. FLIM-FLAMS (Force-Lifted, Timber, Flat-Laminated Shells) are self-assembling timber shells made by etching radial cut patterns into flat sheet goods, which are then laminated together and stretched upward to create rapidly deployable wooden tents. The process utilizes advanced digital software to simulate the deformation of flat geometries cut with computationally optimized radial patterns when lifted from a central axis. Once that geometry is optimized digitally, the flat radial pattern is milled into standard plywood panels, thereby converting flat sheet goods into giant wooden springs, which, when lifted from their center, transform into doubly curved, bending-active vaults.
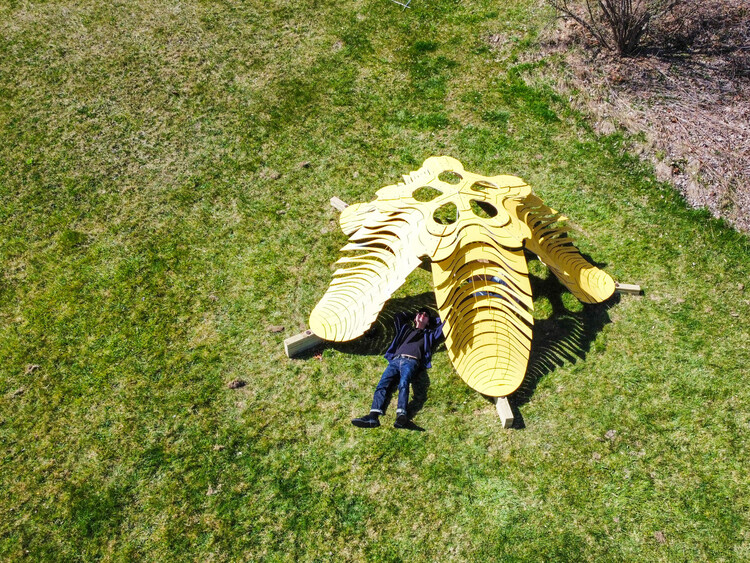
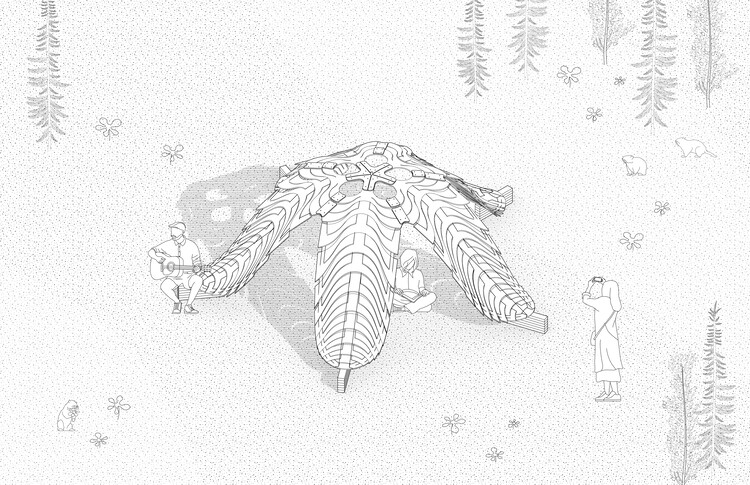
The FLIM-FLAMS process was developed as part of Neal Lucas Hitch’s master’s dissertation at Cornell University’s Department of Design Technology under the guidance of research advisors Sasa Zivkovic and Leslie Lok. It was constructed in partnership with The Soil Factory, a non-profit advocating for experimental sustainable practices in Ithaca, New York.
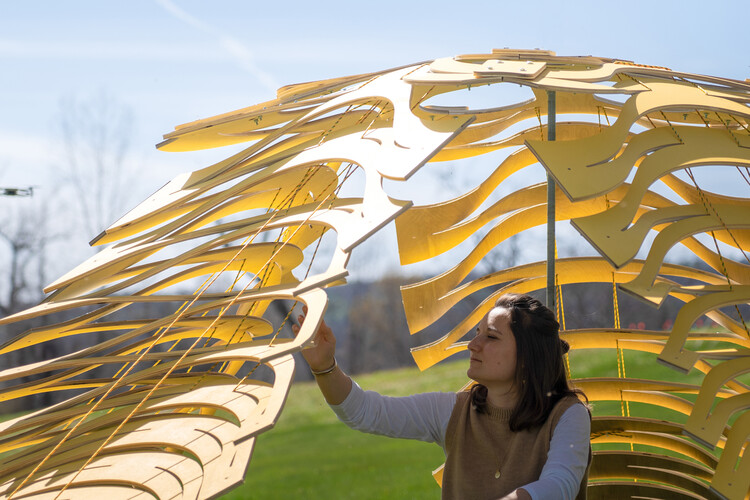
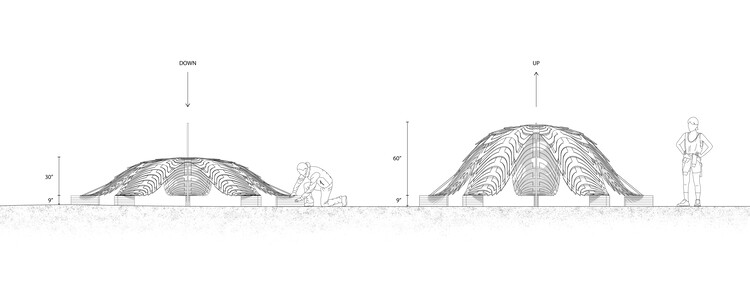
Unlike other standard building materials such as steel, plastic, or concrete, wood cannot be easily molded or cast, making it historically difficult to achieve complex bending with timber components without significant material waste. Conversely, FLAM-FLAMS implements an innovative process in which computational tools are used to bolster hand-building techniques to produce flat-fabricated and rapidly deployable complex timber shells with minimal waste.
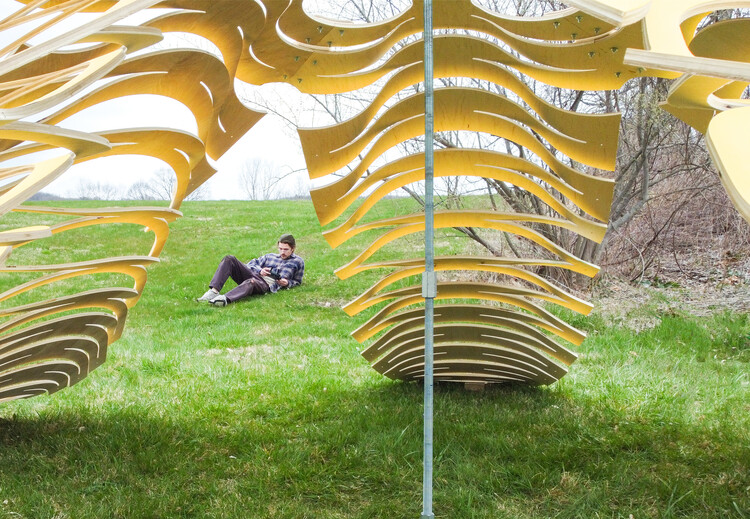
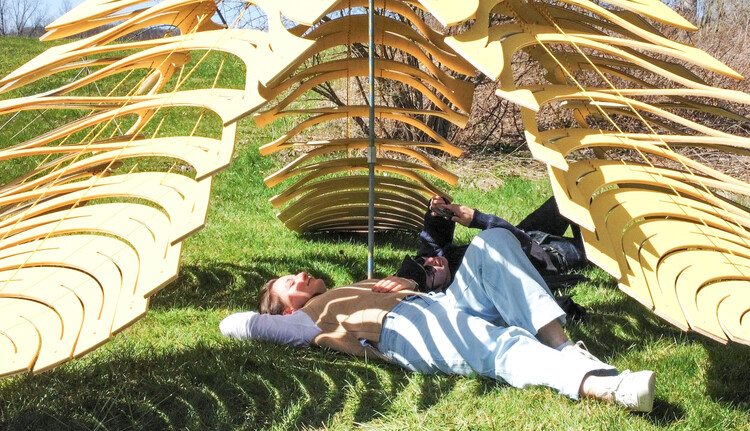
The design of FLIM-FLAMS starts with a computational workflow, coding undulating radial patterns based on biological principles and cutting them into flat geometries. These geometries are then virtually simulated using digital twins to mimic the self-assembly process. The physical construction of FLIM-FLAMS starts by etching the digitally optimized cut pattern into flat plywood sheets using a two-axis CNC mill. Then, the sheets are transported to the site and laminated at their short ends to create a large flat sheet with a diameter of 15 feet. Finally, a hexagonal nut under the plywood is threaded up a central rod, rising 60 inches high. As the nut is lifted, the plywood gradually self-assembles into its final vaulted shape.
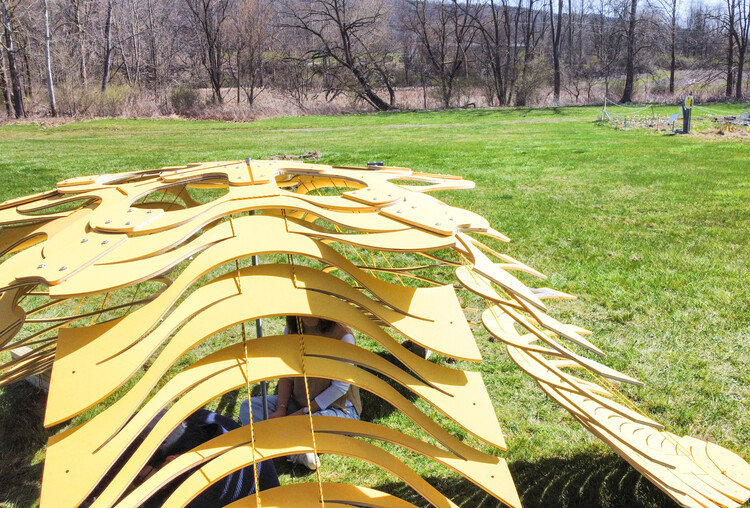
The result is a method for timber construction that transforms wood (a material usually chosen for its rigid properties) into a flexible membrane capable of complex bending. Here, the project demonstrates the versatility of timber to achieve rapidly deployable, multi-curving geometries without the need for excessive material waste typically associated with CNC milling curved timber elements. Furthermore, by combining emerging digital processes with physical construction techniques, the project exemplifies how technological and analog procedures can merge to innovate more sustainable design solutions.